Friday, July 27, 2007
Where is home?
This is something that's been on my list for ages... to get some data on Darwin's optoswitches (H21LOI). How good are they at providing a repeatable home position?

No surprises here - it's all pretty damn accurate. A testament to some solid programming no doubt, nice one ;-) I ran the y-axis back and forwards 10 times, with a caliper strapped on. For both speeds the opto-switch arrangement homed the y-axis to the same motor step 10 out of 10 times. From the results below it's pretty obvious that even greater repeatability might be achieved by slowing the axis down before meeting the end-stop.


No surprises here - it's all pretty damn accurate. A testament to some solid programming no doubt, nice one ;-) I ran the y-axis back and forwards 10 times, with a caliper strapped on. For both speeds the opto-switch arrangement homed the y-axis to the same motor step 10 out of 10 times. From the results below it's pretty obvious that even greater repeatability might be achieved by slowing the axis down before meeting the end-stop.

Friday, July 20, 2007
RepRap Talk Online
Recently, I gave a talk at NYLUG about the RepRap project. An mp3 of the speech is now online for anyone who wants to give it a listen. I think it gives a good overview of the project in general and the ideas behind it.
http://www.archive.org/details/NYLUG_2007_07_11_General_Meeting
http://www.archive.org/details/NYLUG_2007_07_11_General_Meeting
Monday, July 16, 2007
Mendel Preview
We are all working like crazy on RepRap 1.0 "Darwin" of course. But I have an MSc student, Arman Ghandizadehdezfuli, who is looking at Mendel for the future. Here's a video of the prototype extruder changer that he's designed being tested in Darwin. (The slight jerkiness is all from the cheapo webcam software; the actual movements were clean and smooth.)
The idea is to have a row of extruders along one (or more) sides of the machine, and have it pick each up and use it in turn so that many different materials can be incorporated in a single built object.
I had originally thought that each extruder would have its own RepRap controller attached to it. Docking and undocking an extruder would momentarily break, and then re-route, the token ring that allows all the controllers to communicate. But now I think that that would be unreliable. Better to have one controller on the moving carriage, and to connect the drives for the motors and heaters from that to each extruder when it is picked up. The extruder machinery doesn't need clean data during the moment of connection, and so this would be far more robust. Any extruder that needs a controller when it is parked (to keep it at temperature, for example) can have its own controller attached to its docking station that makes contacts in the same way.
Another change will be that the X, Y, and Z flags for the opto endstops will be on each extruder (rather than having just one set on the carriage), so the machine can always zero with precision and get the registration between materials exactly right. The picker-upper grip on the extruder in the carriage is firm, and it doesn't move. But this zeroing scheme would also mean that the grip wouldn't have to grab an extruder in exactly the same place each time.
The idea is to have a row of extruders along one (or more) sides of the machine, and have it pick each up and use it in turn so that many different materials can be incorporated in a single built object.
I had originally thought that each extruder would have its own RepRap controller attached to it. Docking and undocking an extruder would momentarily break, and then re-route, the token ring that allows all the controllers to communicate. But now I think that that would be unreliable. Better to have one controller on the moving carriage, and to connect the drives for the motors and heaters from that to each extruder when it is picked up. The extruder machinery doesn't need clean data during the moment of connection, and so this would be far more robust. Any extruder that needs a controller when it is parked (to keep it at temperature, for example) can have its own controller attached to its docking station that makes contacts in the same way.
Another change will be that the X, Y, and Z flags for the opto endstops will be on each extruder (rather than having just one set on the carriage), so the machine can always zero with precision and get the registration between materials exactly right. The picker-upper grip on the extruder in the carriage is firm, and it doesn't move. But this zeroing scheme would also mean that the grip wouldn't have to grab an extruder in exactly the same place each time.
Labels: extruder changer, multiple materials
Friday, July 06, 2007
Darwin's Adventures Down Under
For those of you wondering why I've been so quiet, a couple of things have happened. First, I lost my job because the New Zealand offices closed. Not happy about that. Nice bunch of people and we worked really well as a team. So, jobhunting is now in order.
Also, because there is a limit to how much jobhunting can be done in a day, I have been assembling a Darwin. I've had to stop due to a shortage of M8 threaded rod, and midnight looms...
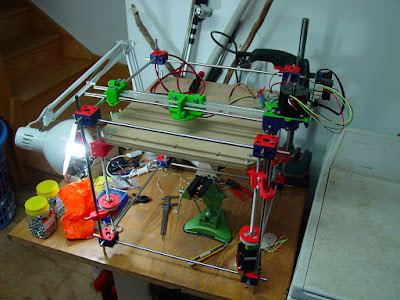
Yes, the bits really are that colourful. Adds a sort of 60's psychedelic feel, I find.
Vik :v)
Also, because there is a limit to how much jobhunting can be done in a day, I have been assembling a Darwin. I've had to stop due to a shortage of M8 threaded rod, and midnight looms...
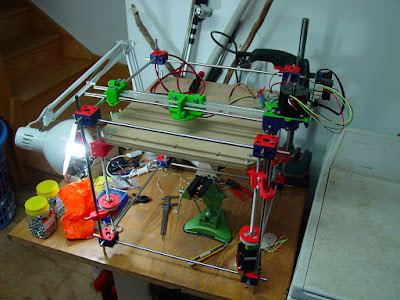
Yes, the bits really are that colourful. Adds a sort of 60's psychedelic feel, I find.
Vik :v)
Labels: darwin, psychedelic, reprap