Wednesday, December 02, 2009
Soluble Support Material
The paste we came up with was based on chalk (we actually used pottery Whiting from the local pottery suppliers that cost a massive £0.67/kg), Ethanol and some PVA Glue. We also used some fancy additives (PEG and Methyl Cellulose) that are typically used in making pastes, but we think we can get rid of these as they didn’t have a massive effect.
Anyway, the final mixture seemed to take a while (at least 15 minutes) to set, but I wondered whether the surface tension and viscosity of the paste would be sufficient to support the usual build material. I created a small block with a shallow hole that didn’t travel through the complete extent of the part, and then built the part with the orientation such that support was needed. I stopped the build at the appropriate point, deposited some paste in the hole before continuing the build. Here is the result:
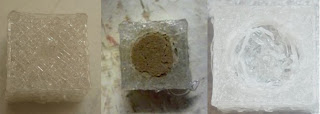
The paste washed away after about a minute when being held under cold water, and it looks like the heat of the plastic was sufficient to cure at least the outer layers of the paste. It’s hard to tell in the photos, but the inside of the hole looks a little messy. I’m not sure if PLA is slightly soluble in the fumes of the Ethanol as the paste sets. It definitely smelt a little weird but I can’t find any data to prove or contradict this suspicion.
A massive thanks goes out to Andrew Dent from the University of Bath materials lab for giving me a hand with all of this.
Edit:
Nophead rightly points out in the comments that this test wasn't entirely fair. The above part could be created anyway by adjusting various parameters. Here is something a bit more fancy:D
It’s apparent that the paste was not completely set as the overhang sags a little bit.
Higher quality pics are available here
If something is worth saying its worth saying twice ;)
But typographical errors aside, this sounds like good news.
Presumably it will have a shelf life but what this is I have no idea. After I used the paste yesterday, I stored it in a small tub with a lid. I've just checked on it and it seems like it hasn't changed at all. I'll leave it on the shelf and check up on it every few days and report back.
Any chance you could link the picture to a bigger version as it is hard to see what's going on.
We can make this shape without any support. I.e. the PLA will simply span the gap because it has support at each side. The results with no support can actually bebetter, the first layer just sags a bit.
A better test would have an edge over the support material which needs to turn a corner. That would show if the filament sticks enough to not get dragged around.
Yes The error with PLA is Ethanol. Its one of the chemicals you need to make a great cosolvent for medical use of PLA.
Yes a cosolvent is to get other chemicals to mix into PLA surface. So the surface layour of PLA and the Paste would be crossing with each other. Not a good thing to be doing.
This might be just too logical. Why use a support material that sets. Not one that is already set.
Common mold systems use like compressed sand or powders. For the simple reason they don't want to set into a solid block and you don't have to wait for them to set.
Also its possible to extract the powder filter it and reuse it. I am sorry I see this path as very wasteful.
made from sugar, melts at 170C and if you make it as dry not 'wet' caramel it gets pretty stiff pretty fast
you would probably need an extruder that can handle granules (would work great with the PLA granules then also
Stay away from Paste materials.
How about this?
5th Generation Strengthen Builds w “Insertion”
http://probersideas.blogspot.com/2009/11/5th-generation-strengthen-builds-w.html
@oiaohm I did think of using powders before. My stumbling block was accurately depositing them. Even if you look at the commercial machines that rely on powder, whether SLS or Zcorp style machines, none of them control the deposition of the powder. They just create a completely flat layer, and then bind certain segments either using the laser or a glue. So the powder is also used as the main build material. It would also need to be operated in an enclosed volume to prevent the powder getting into the mechanics of the machine, requiring a major redesign.
Though I do agree with you that it isn't ideal that the process is wasteful. Obviously we would still try to design parts without the need for support in the first place.
@Prober I strongly recommend you read eD's thesis on the mechanical design of Darwin (its in the documentation section on the main site). There is a rather large study on future materials required to increase the self-replication count. In short, paste materials are the most useful in increasing the replication count i.e. we don't have much choice but go down this route. Although there may be an alternative material that can be used as support.
Also I don't really understand how your "insertion" method overcomes the need for support material.
If the nozzle is unable to get close to the inserted component due to its size, how do you plan to create a good bond between the plastic and the inserted component? I look forward to seeing your results on this anyway!
I suspect that the PLA isn't dissolving in the ethanol, but is swelled by it (cf. pliable Tygon tubing and inflatable vinyl products vs. hard PVC in plumbing and LP records: swelling makes the difference). It is also possible that the ethanol is lysing the PLA chains, making ethyl lactate terminal groups.
@Rhys: My reading of the idea is that the insert would make a shared, flat surface with the printed part, and the new flat surface would be printed over.
@Joel - That makes much more sense but that approach would still only work in a relatively small number of situations that support is useful for.
This approach is very impressive too though! Nice work :)
>>I strongly recommend you read eD's thesis on the mechanical design of Darwin (its in the documentation section on the main site). There is a rather large study on future materials required to increase the self-replication count.<<<
Yes I have briefly, read parts of it. That's one of the reasons I hope to have my ideas of 5th Generation Strengthen Builds w “Insertion”
applied.
Have you read my materials?
(1) Insertion (genetics) From Wikipedia
In genetics, an insertion (also called an insertion mutation) is the addition of one or more nucleotide base pairs into a DNA sequence. This can often happen in microsatellite regions due to the DNA polymerase slipping. Insertions can be anywhere in size from one base pair incorrectly inserted into a DNA sequence to a section of one chromosome inserted into another.
>>>Also I don't really understand how your "insertion" method overcomes the need for support material. <<<<
That's because the insertion materials are the support materials.
The "insertion" method will Make composite parts on RepRap!
>>why not "dry" caramel<<<
>>Yeah, if you start printing caramel parts the toothpick idea might become really usefull!<<
You have the sweet tooth thing going??
Toothpicks might be a great support material. Take three and glue them, or better yet hot glue (nylon)them into a triangle. A very strong "Support Material"
Someone just needs to write the SW to take advantage of the idea and run with it.
Part of my work is getting stuff cast for particular jobs. Think sand castle. It wet it holds it shape until it drys then it becomes insanely soft yet still holds it shape. For metal molding this kind of material is ideal.
Dry application of powders is hard. For removal you avoid using setting compounds it is better. Then you don't need to be washing it away here. Vibration can make the powder return to that.
No rapid prototyping machines I know uses compressed powders or wet powders. Ie skip the glue if you can. The glue only gives you something to deslove later making removing latter more time taking. Glue also makes it harder to recycle the material. Yes the trick is keeping the powder with wet powders at just the right level. Even that both are used in different types of molding.
Yes I do agree the current RepRap operation layout does not suit dry powdered work. mendel is close but you would need to lock the cross board head at top and add a lowering system to the extrude head itself so you could get a box in there.
Wet powder work most likely workable. Compressed powder it simpler with a outer box.
Both wet and compressed powders can be washed out. compressed and wet can be vibrated out when the wet is dry. Both can also be scraped out if something is touch to being washed or vibrated.
Glued limits your removal methods.
Joel you are party right cosolvent is used to mix something else into the material. So swelling is to be expected as the two materials mix. You don't have a nice speration divide.
its stable in a wet state and can dry very quick on the surface..its reusable.
its pretty close to the wet sands thing but because of the fine grain there would be less wear in the mechanics.
by the way it would be nice to print with it anyway.. you can burn it and drink beer out of it afterwarz!
Gelatin 10.0 parts by weight = 25% Potato starch 8.0 parts by weight = 20% Glycerol l.5 parts by weight = 3.75% Purified water 20.5 parts by weight = 51.25%
heating it up in the nozzle will also determine the viscosity i think...
check this:
http://www.freepatentsonline.com/4849246.html
I am building a mendel prusa so I can actually have control over settings, nozzle sizes, materials etc. I was hoping to find a way to add a second extruder for thermoplastic support material similar to what the dimension machine uses, but that requires figuring out what the material is first.
You just have to point very exactly at the place where the NaCl should be, drop some water with high concentration of NaCl and voila!
<< Home