Monday, August 14, 2006
Rethinking everything...
Posts by Sebastien and Simon got me to thinking this morning about RepRap. Sebastian's post led me to recalculate a number I did way back last November and Simon's post made me mad, something I've always found to be a good spur to creative thought. Thanks go to you both. :-)
Sebastien's post was to Vik asking him what the extrusion rate of Da Witch was. Vik guessed at 1 cc/min. I responded doing an envelope calculation which indicated that Vik's calculation was just short of a magnitude off. From the message...
Figuring a 0.8 mm extrusion thread and running at the 4 mm/sec that Mk II was designed for you're getting about 2 mm^2/sec. or 7.24 cc/hr which gives you a modest, but not unreasonable 5.2 kg/month on a constant duty cycle.
Way back last November I made a calculation of extrusion rates when Adrian first published the Mk II extruder. The number I came up with then was 2.83 cc/hr or roughly 2 kg of polymer/month if operated full-time.
It was always obvious to me that 2 kg/month of polymer extrusion for 24x7 operation was just not practical. This morning I realised, however, that my calculation did not allow for the non-Newtonian swelling of the extruded polymer thread. I was figuring that the thread that came out of the Mk II was the same diameter as the orifice. WRONG! Vik has seen that a 0.5 mm orifice yields a 0.8 mm polymer thread.
Now extruding 5.2 kg/month of polymer is a whole different ball game.
That got me to thinking about Godzilla, which I have targeted 20-40 mm/sec extrusion rates. I've learned a lot designing and building Godzilla and at this point I am sure that I can get it to work, probably at about 20 mm/sec. That would extrude something like 26 kg of polymer a month.
There are some practical problems with Godzilla, though.
It's big. It's got a 700x700x350 mm work volume. It's footprint is about 1.5 square meters. It's also loud. Frankenmotors don't scream, but they are full-throated. Two of them running at once will make about as much noise as an electric blender. If you were married you couldn't keep Godzilla in the house with your wife unless she was as committed to 3D prototyping as you are. That's probably an unreasonable filter for guys wanting to marry to put on potential mates. It just wouldn't work. I'm crazy, live by myself, divorced and have a bit of hearing loss from my misspent youth, so Godzilla doesn't bother me. Most people would be bothered, though. As a practical matter Godzilla would have to live in somebody's workshop and it wouldn't be a machine that you'd want to leave running overnight or over the weekend. As a practical matter you're not going to be able to run it for more than about 8 hours/day.
That means that you're only going be extruding about 8.7 kg of CAPA a month with it, that's only 2/3rd's more than Vik's machine. Now it can make lots bigger things than Da Witch, but realistically, how often are you likely to be making huge things with your RepRap?
That's a bitter pill for me, but there it is all the same.
Now let's get to Simon's message that made me mad, but in a creative way. He indicated that servos aren't on for now, that it has to be steppers. Well, I've probably got more hours working with turning brushed DC motors into servos than anybody on the team and I couldn't disagree more. Now Frankenmotors need some work and a lot of thinking to be used properly. The little yellow plastic G4 gearmotor servo is a very different story. Here's why.
You can get steppers surplus for about US$5-10/unit. The moment that RepRap takes off, however, surplus steppers are going to evaporate and people will be paying list price for them, which is about US$50-75/unit. That means that if you are shooting for a US$400 RepRap the steppers are going to cost you 40-60% of that. Parts for stepper boards are also going to cost you another US$15 or so in parts when all is said and done. That means that you're talking about 50-70% of your RepRap budget going for just motors and control boards before you even try to build the positioning stages and extruder. That's just not on.
Now I can buy a yellow plastic G4 gear motor retail for between US$5-6/unit.
http://www.pololu.com/products/solbot/0181/
Add a shaft encoder to that and you've got US$10. That's 20% of the real cost of a stepper. As well, the much lower power draw means that the chips you have to buy to drive the motor are cheaper. Finally, most of the mass and cost of the G4 and it's siblings is in the plastic gear box. The motor itself can be had for maybe US$1.50/unit retail. The rest you can reprap if you want.
What all this means is that the cost of your motors and control boards for gearmotor servos for a Vik-sized RepRap is going to be maybe US$60, and a bit less if you make your own gear boxes.
Now let's do a thought experiment. Let's take Reiyuki's pretty conventional (in CNC terms) gantry design for a wooden RepStrap.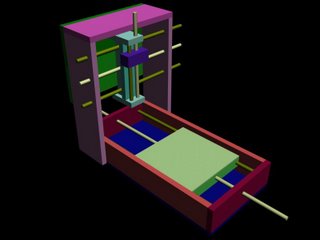
He thoughtfully provides us with a materials quantity survey.
24x48" of 1/8"
48" of 1x2
16" of 1x3
74" of 1x4
78" of 1x6
Doing the numbers you get roughly 17250 cm^3 of materials volume. In wood that gives you about 10 kg of material. In CAPA it would be more like 17.5 kg.
If you redesigned Reiyuki's system for CAPA from the get go you can bring that number down to about 3.5 kg. Pushing it harder you could probably shave another kg off of that, but why bother?
What it all means is that a Reiyuki RepStrap could make a full polymer copy of itself in 20 days.
What it also means is that you could make one for under US$200, everything included... if you went the G4 gearmotor servo route. Double that if you use steppers.
A Reiyuki RepStrap has a 300x600 mm footprint. That's not much worse than most ink-jet printers. Put hoods over those G4's and you will have something that is probably considerably quieter than your ink-jet. Run the whole shebang on 12v power and you're not going to worry about letting it run nights and weekends. Reiyuki's design, when you look at it, isn't all that different than Vik's, which we know works. It uses threaded rods and we don't stress them to the extent Godzilla does. Same general configuration. It scales, too.
If we take my own proclivity for dynamic extruder heads we can probably either reduce the footprint or increase the capacity for a set footprint. I tend to think that G4's running positioning platforms using RepRapped rack and pinions (yes, I've just about got the script running) could make a lighter system still with fewer hard metal parts to buy.
You're can naturally make spare parts for a design like this when you aren't actually using the system for something else. There will be a natural tendency to make spares and keep maybe two systems going for reliability. Two systems not all that much bigger than Vik's have a hell of a lot of extrusion capacity, viz, about 11 kg/month.
The present paradigm has your PC running the RepRap. Put a bigger PIC18F chip in the controller and your PC could handle several RepRaps.
Having spares around is going to give you a natural tendency to help other people get theirs going, too.
Sebastien's post was to Vik asking him what the extrusion rate of Da Witch was. Vik guessed at 1 cc/min. I responded doing an envelope calculation which indicated that Vik's calculation was just short of a magnitude off. From the message...
Figuring a 0.8 mm extrusion thread and running at the 4 mm/sec that Mk II was designed for you're getting about 2 mm^2/sec. or 7.24 cc/hr which gives you a modest, but not unreasonable 5.2 kg/month on a constant duty cycle.
Way back last November I made a calculation of extrusion rates when Adrian first published the Mk II extruder. The number I came up with then was 2.83 cc/hr or roughly 2 kg of polymer/month if operated full-time.
It was always obvious to me that 2 kg/month of polymer extrusion for 24x7 operation was just not practical. This morning I realised, however, that my calculation did not allow for the non-Newtonian swelling of the extruded polymer thread. I was figuring that the thread that came out of the Mk II was the same diameter as the orifice. WRONG! Vik has seen that a 0.5 mm orifice yields a 0.8 mm polymer thread.
Now extruding 5.2 kg/month of polymer is a whole different ball game.
That got me to thinking about Godzilla, which I have targeted 20-40 mm/sec extrusion rates. I've learned a lot designing and building Godzilla and at this point I am sure that I can get it to work, probably at about 20 mm/sec. That would extrude something like 26 kg of polymer a month.
There are some practical problems with Godzilla, though.
It's big. It's got a 700x700x350 mm work volume. It's footprint is about 1.5 square meters. It's also loud. Frankenmotors don't scream, but they are full-throated. Two of them running at once will make about as much noise as an electric blender. If you were married you couldn't keep Godzilla in the house with your wife unless she was as committed to 3D prototyping as you are. That's probably an unreasonable filter for guys wanting to marry to put on potential mates. It just wouldn't work. I'm crazy, live by myself, divorced and have a bit of hearing loss from my misspent youth, so Godzilla doesn't bother me. Most people would be bothered, though. As a practical matter Godzilla would have to live in somebody's workshop and it wouldn't be a machine that you'd want to leave running overnight or over the weekend. As a practical matter you're not going to be able to run it for more than about 8 hours/day.
That means that you're only going be extruding about 8.7 kg of CAPA a month with it, that's only 2/3rd's more than Vik's machine. Now it can make lots bigger things than Da Witch, but realistically, how often are you likely to be making huge things with your RepRap?
That's a bitter pill for me, but there it is all the same.
Now let's get to Simon's message that made me mad, but in a creative way. He indicated that servos aren't on for now, that it has to be steppers. Well, I've probably got more hours working with turning brushed DC motors into servos than anybody on the team and I couldn't disagree more. Now Frankenmotors need some work and a lot of thinking to be used properly. The little yellow plastic G4 gearmotor servo is a very different story. Here's why.
You can get steppers surplus for about US$5-10/unit. The moment that RepRap takes off, however, surplus steppers are going to evaporate and people will be paying list price for them, which is about US$50-75/unit. That means that if you are shooting for a US$400 RepRap the steppers are going to cost you 40-60% of that. Parts for stepper boards are also going to cost you another US$15 or so in parts when all is said and done. That means that you're talking about 50-70% of your RepRap budget going for just motors and control boards before you even try to build the positioning stages and extruder. That's just not on.
Now I can buy a yellow plastic G4 gear motor retail for between US$5-6/unit.
http://www.pololu.com/products/solbot/0181/
Add a shaft encoder to that and you've got US$10. That's 20% of the real cost of a stepper. As well, the much lower power draw means that the chips you have to buy to drive the motor are cheaper. Finally, most of the mass and cost of the G4 and it's siblings is in the plastic gear box. The motor itself can be had for maybe US$1.50/unit retail. The rest you can reprap if you want.
What all this means is that the cost of your motors and control boards for gearmotor servos for a Vik-sized RepRap is going to be maybe US$60, and a bit less if you make your own gear boxes.
Now let's do a thought experiment. Let's take Reiyuki's pretty conventional (in CNC terms) gantry design for a wooden RepStrap.
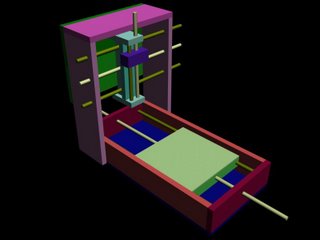
He thoughtfully provides us with a materials quantity survey.
24x48" of 1/8"
48" of 1x2
16" of 1x3
74" of 1x4
78" of 1x6
Doing the numbers you get roughly 17250 cm^3 of materials volume. In wood that gives you about 10 kg of material. In CAPA it would be more like 17.5 kg.
If you redesigned Reiyuki's system for CAPA from the get go you can bring that number down to about 3.5 kg. Pushing it harder you could probably shave another kg off of that, but why bother?
What it all means is that a Reiyuki RepStrap could make a full polymer copy of itself in 20 days.
What it also means is that you could make one for under US$200, everything included... if you went the G4 gearmotor servo route. Double that if you use steppers.
A Reiyuki RepStrap has a 300x600 mm footprint. That's not much worse than most ink-jet printers. Put hoods over those G4's and you will have something that is probably considerably quieter than your ink-jet. Run the whole shebang on 12v power and you're not going to worry about letting it run nights and weekends. Reiyuki's design, when you look at it, isn't all that different than Vik's, which we know works. It uses threaded rods and we don't stress them to the extent Godzilla does. Same general configuration. It scales, too.
If we take my own proclivity for dynamic extruder heads we can probably either reduce the footprint or increase the capacity for a set footprint. I tend to think that G4's running positioning platforms using RepRapped rack and pinions (yes, I've just about got the script running) could make a lighter system still with fewer hard metal parts to buy.
You're can naturally make spare parts for a design like this when you aren't actually using the system for something else. There will be a natural tendency to make spares and keep maybe two systems going for reliability. Two systems not all that much bigger than Vik's have a hell of a lot of extrusion capacity, viz, about 11 kg/month.
The present paradigm has your PC running the RepRap. Put a bigger PIC18F chip in the controller and your PC could handle several RepRaps.
Having spares around is going to give you a natural tendency to help other people get theirs going, too.
Comments:
<< Home
I had a feeling my posting might inspire you :)
I think the DC motor goal is great. It has the potential to increase the output rate. I'm sure you agree that it is more complex than dealing with steppers, so the question is really just how much more complex and how managable that complexity is. There are lots of factors that affect this.
With a stepper motor that is sufficiently engineered for the task, for practical purposes you can essentially assume instant acceleration. With a DC motor, there is a bit of an acceleration curve that you have to deal with. What's worse is that the curve is different for each axis. That makes coordinating the axes for the very fine features comparitively difficult.
You have to contend with the startup burst you typically get from a DC motor too.
You can reduce the acceleration curve by using beafier motors and more gearing. At some point, a sufficiently beafy motor reduces complexity closer to that of a stepper motor.
If you have a large machine, it makes that level even harder to achieve.
I'm not quite sure how big a motor you need before it becomes similarly easy. And I suspect even then that the more dynamic motion of the DC motor will throw in some surprises you didn't expect.
So more smaller machines is a great way to go because it reduces the motor requirements and costs. Paralleling is a good way to produce more.
Smaller, cheaper, more... It's not the first time it's been raised. RepRap is really all about using higher machine counts and lower costs for faster production. That applies for both DC and stepper designs.
I look forward to a working DC motor positioning system. My personal opinion of achieving high levels of accuracy with DC motors is that it is considerably more complex and I am doubtful we will have a good solution by the time we want to release RepRap version 1.0. I strongly hope I am wrong and I would very much welcome somebody proving me wrong because it would be good for everybody.
I think the DC motor goal is great. It has the potential to increase the output rate. I'm sure you agree that it is more complex than dealing with steppers, so the question is really just how much more complex and how managable that complexity is. There are lots of factors that affect this.
With a stepper motor that is sufficiently engineered for the task, for practical purposes you can essentially assume instant acceleration. With a DC motor, there is a bit of an acceleration curve that you have to deal with. What's worse is that the curve is different for each axis. That makes coordinating the axes for the very fine features comparitively difficult.
You have to contend with the startup burst you typically get from a DC motor too.
You can reduce the acceleration curve by using beafier motors and more gearing. At some point, a sufficiently beafy motor reduces complexity closer to that of a stepper motor.
If you have a large machine, it makes that level even harder to achieve.
I'm not quite sure how big a motor you need before it becomes similarly easy. And I suspect even then that the more dynamic motion of the DC motor will throw in some surprises you didn't expect.
So more smaller machines is a great way to go because it reduces the motor requirements and costs. Paralleling is a good way to produce more.
Smaller, cheaper, more... It's not the first time it's been raised. RepRap is really all about using higher machine counts and lower costs for faster production. That applies for both DC and stepper designs.
I look forward to a working DC motor positioning system. My personal opinion of achieving high levels of accuracy with DC motors is that it is considerably more complex and I am doubtful we will have a good solution by the time we want to release RepRap version 1.0. I strongly hope I am wrong and I would very much welcome somebody proving me wrong because it would be good for everybody.
One small point - if you have a screw drive with a 1mm pitch, the a servo only needs to hit an angle of 36 degrees to get 0.1mm accuracy... My little DC servo that I put on the wiki here can easily hit an accuracy 10 times better than that.
I agree with you both - steppers to start with, servos for the future. Close that control loop.
And I bet that HP don't pay what we do for the steppers they put in their printers...
I agree with you both - steppers to start with, servos for the future. Close that control loop.
And I bet that HP don't pay what we do for the steppers they put in their printers...
The only hassle with the GM4 that both you and I used to develop servo boards and firmware is that it has a max rotation of 70 rpm which works out at less than 1.2 rps which gives you 1.2 mm/sec translation for that power screw. We've got to move a little faster than that. :-)
Belt drive will go faster. But right now, we need something that works, and screw thread seems to be it.
Vik :v)
Vik :v)
***And I bet that HP don't pay what we do for the steppers they put in their printers...***
No, but then we're not buying 100,000 at a time, either. :-(
No, but then we're not buying 100,000 at a time, either. :-(
Mad? MAD?? Plaasjaapie, is that why you were mentioning Tesla coils? ;)
Uh, I have a confession to make...
After mulling over ideas inspired by Godzilla/Da Witch and a gaggle of CNC subtractive machines, I started focusing on cheap and small for several reasons. For example, you can RepRap small intricate connecting parts, and then cut and add in big lengths of metal or wood elements to make a larger machine (not quite pure RepRapping, but it would work for me).
A while back I tried my best to shoot down Forrest's idea of using a DC motor and gears. Over the last week I've been planing/building a testbed that uses DC motors and gears (salvaged cordless screwdrivers no less). I felt like a true hypocrite! ;)
But... the idea was to move to steppers after. If the geared units couldn't cut it, as I was expecting them not too, given the slack in the gear train.
But... as of now I'm thinking that could be worked around since learing more from hanging around and seeing how you guys are solving some of the techincal problems. I suspect, if there are two rotation/movement sensors, one low res unit on the motor, and a higher res unit on the gear output (or on a static ruler-like side strip), one could dynamically manage the slack and momentum issues. Given as how MCUs are progressing and dropping in price, managing such an awkward setup might not be expensive.
As a side note, I'm pleased to see progress on rack and pinions. Threaded rods are very inefficient, the threads are ment to bind, not slide, hence that forces the use of bigger motors. Square profile threaded rods are not commonly available, and recirculating ball nuts which are even more efficient are very expensive.
Okay, enough conjecture for now, must go make concrete so the kids don't fall out of the house...
Uh, I have a confession to make...
After mulling over ideas inspired by Godzilla/Da Witch and a gaggle of CNC subtractive machines, I started focusing on cheap and small for several reasons. For example, you can RepRap small intricate connecting parts, and then cut and add in big lengths of metal or wood elements to make a larger machine (not quite pure RepRapping, but it would work for me).
A while back I tried my best to shoot down Forrest's idea of using a DC motor and gears. Over the last week I've been planing/building a testbed that uses DC motors and gears (salvaged cordless screwdrivers no less). I felt like a true hypocrite! ;)
But... the idea was to move to steppers after. If the geared units couldn't cut it, as I was expecting them not too, given the slack in the gear train.
But... as of now I'm thinking that could be worked around since learing more from hanging around and seeing how you guys are solving some of the techincal problems. I suspect, if there are two rotation/movement sensors, one low res unit on the motor, and a higher res unit on the gear output (or on a static ruler-like side strip), one could dynamically manage the slack and momentum issues. Given as how MCUs are progressing and dropping in price, managing such an awkward setup might not be expensive.
As a side note, I'm pleased to see progress on rack and pinions. Threaded rods are very inefficient, the threads are ment to bind, not slide, hence that forces the use of bigger motors. Square profile threaded rods are not commonly available, and recirculating ball nuts which are even more efficient are very expensive.
Okay, enough conjecture for now, must go make concrete so the kids don't fall out of the house...
I actually really think that brushed DC motors aren't the way to go in the long term. What I think would be ideal is a brushless DC motor - which is to say, a low resolution stepper designed to spin continuously. The only difference is that they are controlled caring about the rate of spin, rather than the position, and that they are optimised for spinning. They also strike me as exceedingly RP-able; a while back I was experimenting halfheartedly with building them with machine screws for magnet cores and 1/4"x1/16" neodymium-iron-boron disk magnets, and the only real reason I stopped was school. It seems to me that one could be fairly easily built into the hub of an RP-ed gear or with a tapped hole through the middle, to make a linear slide...
That's what I think will be going on once there are repraps out and about for people to develop them with. First thing I'm thinking of doing is a coil winding machine... basic, functional design of brushless motors is not the craziest thing in the world.
That's what I think will be going on once there are repraps out and about for people to develop them with. First thing I'm thinking of doing is a coil winding machine... basic, functional design of brushless motors is not the craziest thing in the world.
*** No, but then we're not buying [stepper motors] 100,000 at a time, either. :-( ***
Not yet, not yet...
Not yet, not yet...
I don't question the ability of a DC motor to accurately position. What I question more is the ease of doing it quickly on multiple axes simultaneously in such a way that you can accurately control movement along any desired path while in motion. The dynamics become more complex then than in the simple case of 1 dimensional movement.
I'm sure it's possible and we'll get there eventually, but it's a whole lot harder than doing it with steppers, which is really pretty trivial. I like trivial.
I'm sure it's possible and we'll get there eventually, but it's a whole lot harder than doing it with steppers, which is really pretty trivial. I like trivial.
Nice to see my 'plans' going to good use. I suspect the 20 day replication could be scaled down a lot, since the dimensions chosen were mostly for their ease-of-purchase. Skimming the polymer down to 1/4" thick might cut the replication down to 7 days using your guestimates, with hopefully minimal loss of accuracy.
BTW: I should be getting back from travel on the Aug21, and I'll probably be itching to get that built asap.
BTW: I should be getting back from travel on the Aug21, and I'll probably be itching to get that built asap.
Simon, yes trivial is good! Truth is, the first fully functional RepRap will have steppers and threaded rods!
jonored, I like your ideas, embeded motors are full of potential. Plaasjaapie is working on a orientable extrusion head, and that would be a great combo.
reiyuki, hey if someone was replicating your machine, all sorts of cavities and webing could be added to the structural parts, making it much faster to make. Just cutting it down to 1/4 inch might make it too flexible...
jonored, I like your ideas, embeded motors are full of potential. Plaasjaapie is working on a orientable extrusion head, and that would be a great combo.
reiyuki, hey if someone was replicating your machine, all sorts of cavities and webing could be added to the structural parts, making it much faster to make. Just cutting it down to 1/4 inch might make it too flexible...
A couple of points: has anyone other than me thought of stripping old printers for their steppers?
And secondly, thinking of the Repstrap, how well would a RepRap with a saw blade in its jaws do woodworking? As Yves points out, if you can 'rap out all the fine parts in plastic, why not do the crude structural ones in wood?
Wood is versatile, available, recyclable and renewable, after all. A RepRap is essentially a CNC machine with an extrusion head for plastic deposition. Removable tool-heads are clearly going to be necessary, so why not?
The only reasons I see against it is that woodworking is quite force-intensive, if that is a word. The whole rationale of additive reprapping rather than subtractive reprapping was, IIRC, to minimise the forces involved, so this may be off-course.
Mind you, subtraction still has some attraction to me in a medium like a plastic where the offcuts just go right back in the hopper. However, you'll always have to lay stuff down in the end - electrical and electronic circuits being exhibit A - so you need an extruder head. Now, the subtractor machine will certainly be able to carry, position and power the extruder, in fact it'll be overspecified for it. Easier to do it that way around..
Alternatively, this might be best dealt with in an "ecosystem" solution - there are already perfectly good subtractive machine tools, including highly available options like those signwriters we were speaking of, and for woodworking you can always grab a handsaw failing all else. Perhaps better to leave subtraction to the rest of the workshop.
Finally, to terminate the bloviatin', 12VDC power would be nice because it fits well in a small-scale, renewable/generator-plus-battery electrical system. The sort of thing you have on a boat, and also the fastest way to get power in the global outback - or in a climate and energy-conscious future London, for that matter. If you can recycle the plastic and circuitry metal, and the other main material is wood, then all you need is a Rutland 913 turbine and some lead-acid batteries for a closed-loop tool chain.
And secondly, thinking of the Repstrap, how well would a RepRap with a saw blade in its jaws do woodworking? As Yves points out, if you can 'rap out all the fine parts in plastic, why not do the crude structural ones in wood?
Wood is versatile, available, recyclable and renewable, after all. A RepRap is essentially a CNC machine with an extrusion head for plastic deposition. Removable tool-heads are clearly going to be necessary, so why not?
The only reasons I see against it is that woodworking is quite force-intensive, if that is a word. The whole rationale of additive reprapping rather than subtractive reprapping was, IIRC, to minimise the forces involved, so this may be off-course.
Mind you, subtraction still has some attraction to me in a medium like a plastic where the offcuts just go right back in the hopper. However, you'll always have to lay stuff down in the end - electrical and electronic circuits being exhibit A - so you need an extruder head. Now, the subtractor machine will certainly be able to carry, position and power the extruder, in fact it'll be overspecified for it. Easier to do it that way around..
Alternatively, this might be best dealt with in an "ecosystem" solution - there are already perfectly good subtractive machine tools, including highly available options like those signwriters we were speaking of, and for woodworking you can always grab a handsaw failing all else. Perhaps better to leave subtraction to the rest of the workshop.
Finally, to terminate the bloviatin', 12VDC power would be nice because it fits well in a small-scale, renewable/generator-plus-battery electrical system. The sort of thing you have on a boat, and also the fastest way to get power in the global outback - or in a climate and energy-conscious future London, for that matter. If you can recycle the plastic and circuitry metal, and the other main material is wood, then all you need is a Rutland 913 turbine and some lead-acid batteries for a closed-loop tool chain.
I have a good collection of steppers from old printers. I am using some of them in my RepStrap. It's a great source, because you can often pick them up for a couple of dollars at a junk shop, or nothing at all if you're in the right place at the right time.
You'll be pleased to know many people are thinking along the same lines as you. 12V is the power supply we're currently developing for.
You'll be pleased to know many people are thinking along the same lines as you. 12V is the power supply we're currently developing for.
Alex, you touched on several good points. It's much harder to build a subtractive machine, the structure and powertrain have to be much more massive and stiff. Any slack will make the cutting tool wobble, unless it's something uber cool (kul!?) like a laser, water jet or electrical discharge.
BTW, I'm also salvaging old printers parts. I suspect if the RepRap thing -really- takes off (and Dr Bowyer gets Knighted) that the second hand stepper market will dry up, only to be flooded by much cheaper new motors right after!
BTW, I'm also salvaging old printers parts. I suspect if the RepRap thing -really- takes off (and Dr Bowyer gets Knighted) that the second hand stepper market will dry up, only to be flooded by much cheaper new motors right after!
Actually, wire-EDM machines require very little force to push the wire into the material.
You could make a wire-EDM chopsaw, maybe? Although we were thinking a scrollsaw. Here's a quickly-googled introduction to wire-EDM:
http://www.moldmakingtechnology.com/articles/020403.html
I've been talking with the emc guys
http://linuxcnc.org/
and the folk in the CAD_CAM_EDM_DRO mailing list
http://groups.yahoo.com/group/CAD_CAM_EDM_DRO/
about making a wire-EDM head for a reprap. Perhaps I should write the idea up in a blog entry.
You could make a wire-EDM chopsaw, maybe? Although we were thinking a scrollsaw. Here's a quickly-googled introduction to wire-EDM:
http://www.moldmakingtechnology.com/articles/020403.html
I've been talking with the emc guys
http://linuxcnc.org/
and the folk in the CAD_CAM_EDM_DRO mailing list
http://groups.yahoo.com/group/CAD_CAM_EDM_DRO/
about making a wire-EDM head for a reprap. Perhaps I should write the idea up in a blog entry.
Now you're talking. May I suggest one of those wire saws sold for outdoor/survival applications could help as the blade? The good ones are very good (but the crap ones..). Some points that brings up - the motor would probably have to go on the head. What else could we do with a powered head?
Note that, if the wire is a consumable, it will probably have to reside on the head as well - can anyone imagine threading it from a reel through the workings of a reprap? Disaster waiting to happen.
On the other hand, some time ago there was a discussion on this blog about wire-welding and soldering techniques that could be used to deposit metal circuits and structures. There would seem to be a bit of read-across between feeding a wire-EDM cutter with wire and feeding a wire metal-depositing head.
Broadly speaking, a big question in all this is how automatic the reprap will be in operation. If you assume that a human operator will usually be nearby, it's far more reasonable to design a precision structure and powertrain to position the head accurately, then do a number of interchangeable tools - plastic/solder extruder, fine printer, cutter/Afghan lathe/drill, etc, each one with its own software profile.
If the thing has to run without much human intervention, modularity is much harder; the control routines for changing heads would be horrible. That means that the tool head must be far more capable and the design process for anything it makes must be dominated by the need to make as much as possible out of extruded plastic.
Post a Comment
Note that, if the wire is a consumable, it will probably have to reside on the head as well - can anyone imagine threading it from a reel through the workings of a reprap? Disaster waiting to happen.
On the other hand, some time ago there was a discussion on this blog about wire-welding and soldering techniques that could be used to deposit metal circuits and structures. There would seem to be a bit of read-across between feeding a wire-EDM cutter with wire and feeding a wire metal-depositing head.
Broadly speaking, a big question in all this is how automatic the reprap will be in operation. If you assume that a human operator will usually be nearby, it's far more reasonable to design a precision structure and powertrain to position the head accurately, then do a number of interchangeable tools - plastic/solder extruder, fine printer, cutter/Afghan lathe/drill, etc, each one with its own software profile.
If the thing has to run without much human intervention, modularity is much harder; the control routines for changing heads would be horrible. That means that the tool head must be far more capable and the design process for anything it makes must be dominated by the need to make as much as possible out of extruded plastic.
<< Home