Tuesday, August 15, 2006
Rack those pinions...
Got it! 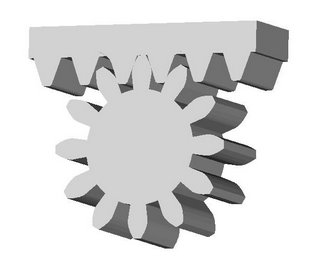
The LuleƄ involute gear script gears and the Kiplinger racks script match up perfectly. I ran the y-zero line for the rack through the pressure radius so that it would be easy to line up gears and racks to check to see if they mated properly.
To check you just make your rack and when doing so specify the number of teeth you want in the pinion. Also make sure that you use the same pressure radius. Once you have your rack done you then make your involute profile gear.
One thing to remember is that if you want to match up your pinion gear with your rack to always specify an even number of teeth in the rack. The reason for this is that the Involute Profile Gear script always places a gear tooth pointing straight up so you need a gap in the rack teeth to seat it without a lot of drama. Once you've done that just select your gear profile and click "object layout". Drop the gear profile in the Y-direction by a value equal to your pressure radius and you will be able to see in an instant whether or not you have a match. It's a dead easy way to avoid design errors.
Half a dozen more scripts like this and AoI will be a proper engineering design CAD system. :-D
I was thinking about short-term, unintended consequences of RepRap this morning. If I remember correctly one of the big problems in engineering education is getting students hands-on time with machine tools so that they can get some experience about where CAD design leaves off and real mechanisms begin. Machine shops and their staff are extremely expensive in my experience and students rarely if ever rate shop time just to tinker with designs.
It seems to me that RepRap would make it possible to put a good prototyping system in any mechanical engineering student's dorm room. The notion of what a RepRap would do towards improving a mechanical engineering student's experience with actually designing mechanisms completely boggles my mind. A student working with a RepRap could easily leave university with more hands-on design experience than a graduate engineer currently picks up in several years in the field. That's noteworthy to say the least. It would make engineering education both better and cheaper. In commonwealth countries it would mean lots more better trained engineers, never mind in the UK.
That alone, Adrian, should get you at least a knighthood and if the world were a fair place a peerage. A professorship would also seem the least that could happen. I don't know if you've ever entertained those sorts of ambitions, but there it is.
You can get both the Rack and the matching Involute Profile Gear scripts at...
http://www.sanma12.com/reprap/software/AoI Scripts/
For you AoI newbies you put these in the "Tools" folder that you find in your "Scripts" folder for Art of Illusion (AoI).
You have to restart AoI before you will be able to see them in the "Scripts" entry in the "Tools" pull-down menu.
One thing Professor Adamson at Lunds Technical University taught me was that the fastest way to see if you had bugs in computer code was to test extreme examples. Here is one.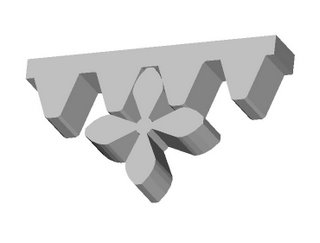
Looks good. :-)
One thing I have noticed is that you need to keep an eye on the AoI extruder facility when you are extruding your rack. Occasionally it will put a little two dimensional web across part of the bottom of one of your rack teeth. You can generally see it as a wrinkle in the sides of the rack when you view it in AoI. I don't know why that is, but you should look out for it. I've found that increasing or decreasing the number of teeth in the rack makes it go away... for now...
Please remember that while the Involute Profile Gear script has been knocked around a bit, the Rack script is a very early beta release. Please let me know if you find any problems with it. Thanks! :-)
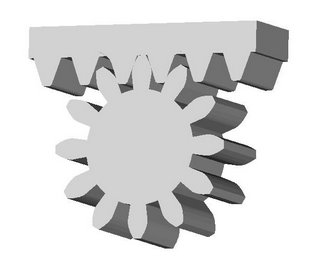
The LuleƄ involute gear script gears and the Kiplinger racks script match up perfectly. I ran the y-zero line for the rack through the pressure radius so that it would be easy to line up gears and racks to check to see if they mated properly.
To check you just make your rack and when doing so specify the number of teeth you want in the pinion. Also make sure that you use the same pressure radius. Once you have your rack done you then make your involute profile gear.
One thing to remember is that if you want to match up your pinion gear with your rack to always specify an even number of teeth in the rack. The reason for this is that the Involute Profile Gear script always places a gear tooth pointing straight up so you need a gap in the rack teeth to seat it without a lot of drama. Once you've done that just select your gear profile and click "object layout". Drop the gear profile in the Y-direction by a value equal to your pressure radius and you will be able to see in an instant whether or not you have a match. It's a dead easy way to avoid design errors.
Half a dozen more scripts like this and AoI will be a proper engineering design CAD system. :-D
I was thinking about short-term, unintended consequences of RepRap this morning. If I remember correctly one of the big problems in engineering education is getting students hands-on time with machine tools so that they can get some experience about where CAD design leaves off and real mechanisms begin. Machine shops and their staff are extremely expensive in my experience and students rarely if ever rate shop time just to tinker with designs.
It seems to me that RepRap would make it possible to put a good prototyping system in any mechanical engineering student's dorm room. The notion of what a RepRap would do towards improving a mechanical engineering student's experience with actually designing mechanisms completely boggles my mind. A student working with a RepRap could easily leave university with more hands-on design experience than a graduate engineer currently picks up in several years in the field. That's noteworthy to say the least. It would make engineering education both better and cheaper. In commonwealth countries it would mean lots more better trained engineers, never mind in the UK.
That alone, Adrian, should get you at least a knighthood and if the world were a fair place a peerage. A professorship would also seem the least that could happen. I don't know if you've ever entertained those sorts of ambitions, but there it is.
You can get both the Rack and the matching Involute Profile Gear scripts at...
http://www.sanma12.com/reprap/software/AoI Scripts/
For you AoI newbies you put these in the "Tools" folder that you find in your "Scripts" folder for Art of Illusion (AoI).
You have to restart AoI before you will be able to see them in the "Scripts" entry in the "Tools" pull-down menu.
One thing Professor Adamson at Lunds Technical University taught me was that the fastest way to see if you had bugs in computer code was to test extreme examples. Here is one.
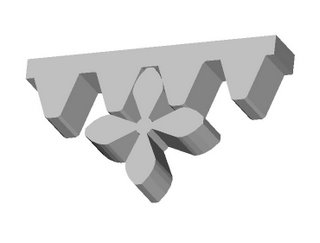
Looks good. :-)
One thing I have noticed is that you need to keep an eye on the AoI extruder facility when you are extruding your rack. Occasionally it will put a little two dimensional web across part of the bottom of one of your rack teeth. You can generally see it as a wrinkle in the sides of the rack when you view it in AoI. I don't know why that is, but you should look out for it. I've found that increasing or decreasing the number of teeth in the rack makes it go away... for now...
Please remember that while the Involute Profile Gear script has been knocked around a bit, the Rack script is a very early beta release. Please let me know if you find any problems with it. Thanks! :-)
Comments:
<< Home
//It seems to me that RepRap would make it possible to put a good prototyping system in any mechanical engineering student's dorm room.//
I can just see it: One RepRap Per Child.
I can just see it: One RepRap Per Child.
Yup, the only thing the engineering school would need to do is to put in a filament maker for their students' convenience. :-)
Great stuff. I think this is going to be really handy for eliminating some externally sourced parts.
Very cool...
Very cool...
Plaas, there's your rack and pinion nicely animated, even showing the 14.5 degree angle!
http://brockeng.com/mechanism/RackNPinion.htm
You probably spotted it, it was with those links you put up for the straight line generators. I just thought it was cool to post for others to see.
http://brockeng.com/mechanism/RackNPinion.htm
You probably spotted it, it was with those links you put up for the straight line generators. I just thought it was cool to post for others to see.
Yup. If you look on that page you'll see that Kiplinger links you to the PDF on method that I used to do the rack polygon. :-D
Post a Comment
<< Home