Monday, July 24, 2006
What we might make with a reprap...
I'm expanding a post that Alex made to my last blog entry because it gives an idea of what one can get up to with a 3D prototyper. The famed Lockheed "Skunk Works" that produced such aircraft as the U2, the SR-71 Blackbird, the F-117 stealth fighter and a variety of other air and spacecraft whose details have never been made public has now created a new UAV called the "Polecat".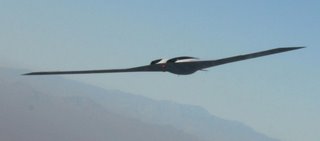
According to the New Scientist...
About 90 per cent of Polecat is made of composite materials with much of that material made by rapid prototyping.
Why? It's cheaper than conventional construction methods for very much the same reasons that we've been talking about...
This use of rapid prototyping is certainly a revolutionary approach to making an aircraft," says Bill Sweetman, aerospace and technology editor of Jane's International Defence Review. "The classic way is to set up a production line with very heavy-duty fixed metal tools that hold everything in the right place." That is too expensive an approach for the low production runs that reconnaissance UAVs are likely to need, he says.
The Polecat was recently shown off at the Farnborough Air Show.
I think that we're in very good company here. :-D
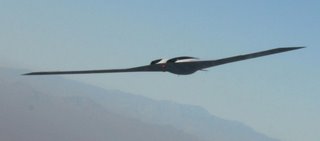
According to the New Scientist...
About 90 per cent of Polecat is made of composite materials with much of that material made by rapid prototyping.
Why? It's cheaper than conventional construction methods for very much the same reasons that we've been talking about...
This use of rapid prototyping is certainly a revolutionary approach to making an aircraft," says Bill Sweetman, aerospace and technology editor of Jane's International Defence Review. "The classic way is to set up a production line with very heavy-duty fixed metal tools that hold everything in the right place." That is too expensive an approach for the low production runs that reconnaissance UAVs are likely to need, he says.
The Polecat was recently shown off at the Farnborough Air Show.
I think that we're in very good company here. :-D
Comments:
<< Home
Sometimes I wonder why over the years I drifted from robots to CNC machines to the RepRap project, and articles like those point out why this seems more interesting and openended.
My personal favorite is the "ShrinkRap" it would be a version of the RepRap that gets smaller and smaller every time you make a new copy. I know you guys are trying to -avoid- global scaling, but I'm wondering how it could be amplified!
"Honey, who opened the RepRap jar?! Now they're replicating all over the kitchen floor!"
:)
My personal favorite is the "ShrinkRap" it would be a version of the RepRap that gets smaller and smaller every time you make a new copy. I know you guys are trying to -avoid- global scaling, but I'm wondering how it could be amplified!
"Honey, who opened the RepRap jar?! Now they're replicating all over the kitchen floor!"
:)
There has been considerable discussion within the RepRap team on how to use a RepRap to build a bigger RepRap and how to use a RepRap to create a more accurate RepRap.
I think you are confusing thermoplastic polymers and thermosetting ones.
The thermoplastic rapid prototyping that RepRap performs is vastly different to the thermosetting composites employed in the article mentioned.
Post a Comment
The thermoplastic rapid prototyping that RepRap performs is vastly different to the thermosetting composites employed in the article mentioned.
<< Home