Wednesday, June 14, 2006
Thinking about making filament again...
Okay, I have a couple of days till the PIC's arrive and Vik brought up the point of there being a developing need for filament production, so I've been thinking about it enough the I want to throw out what may be an approach for you all.
As you know, I was very excited about and did a lot of work on an auger extruder for filament. I got unexcited instantly when I found out how much better filament a simple piston design did the job.
The auger design I did requires powdered polymer unless you go up to the sort of auger diameters that Adrian used. As well, the auger design that I did wanted being broken down and cleaned practically every time you used it if you wanted good results. It also had problems with bridging of polymer powder jamming the feed hopper and any number of other maladies. It was basically German design, attractive but complicated and requiring rather careful use when what we need is Russian design, primitive, ugly and utterly reliable.
What I was using looked very much like a standard ASTM standard test rig for determining polymer melt index.
I got the illustration from a lab manual used up at McMaster University. You can see the full document here.
http://chemeng.mcmaster.ca/courses/che4l2/labmodules/polymer.pdf
It's a nice concept except that it's a one shot device and looks to be a pig to use on a production basis if the user's manual is any guide.
Adrian was talking about using a pressure cooker some time ago and I had thought along the same lines as well. Taking the bare essentials from that idea, what would happen if we just tossed our scrap CAPA in a pot and heated it. Don't get lost in the details of how to heat the pot just yet, just assume that we can do it without scorching.... use a double boiler or something. :-)
Okay, so we've got this heated pot of scrap polymer. After a while the bits melt into a big puddle, the polymer slumps down (very slowly given its viscosity) . Now suppose we've drilled a hole in the side of the pot way down at the bottom well under the level of the molten polymer.
Then we start plumbing up a two stroke pump using Adrian's favourite plumbing parts. :-)
Here's roughly what the intake stroke looks like...
Pardon the illustration. I drew it on my white board and photographed it. That's not a great presentation method, but I'm in a hurry.
Your pot's on the left and the piston of your pump is driven by a gear motor that runs a threaded rod arrangement. I didn't get too specific on how that all fits together. At this point what is relevant is that we have what amounts to a linear motor that can deliver a LOT of thrust.
You can see two spring loaded back pressure valves. On the intake stroke the valve to the pot opens up letting the polymer melt be drawn in as the piston is pulled upwards in the cylinder.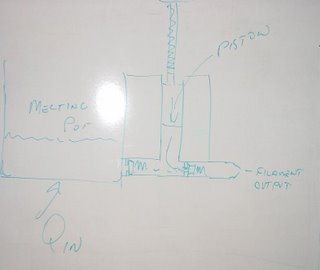
Once your cylinder is full you reverse the rotation of the gear motor which closes the back pressure valve into the pot and opens the valve to the extruder tip.
That's basically it.
What's nice is that this system can operate VERY slowly to take into account the high viscosity of the polymer melt. It can also extrude specific amounts of polymer with a high degree of accuracy. Knowing the mass flow rate of polymer out of the extruder on a real-time basis lets us control a conveyer that takes the extruded polymer away.
That's my first cut at a filament extruder.
As you know, I was very excited about and did a lot of work on an auger extruder for filament. I got unexcited instantly when I found out how much better filament a simple piston design did the job.
The auger design I did requires powdered polymer unless you go up to the sort of auger diameters that Adrian used. As well, the auger design that I did wanted being broken down and cleaned practically every time you used it if you wanted good results. It also had problems with bridging of polymer powder jamming the feed hopper and any number of other maladies. It was basically German design, attractive but complicated and requiring rather careful use when what we need is Russian design, primitive, ugly and utterly reliable.
What I was using looked very much like a standard ASTM standard test rig for determining polymer melt index.

I got the illustration from a lab manual used up at McMaster University. You can see the full document here.
http://chemeng.mcmaster.ca/courses/che4l2/labmodules/polymer.pdf
It's a nice concept except that it's a one shot device and looks to be a pig to use on a production basis if the user's manual is any guide.
Adrian was talking about using a pressure cooker some time ago and I had thought along the same lines as well. Taking the bare essentials from that idea, what would happen if we just tossed our scrap CAPA in a pot and heated it. Don't get lost in the details of how to heat the pot just yet, just assume that we can do it without scorching.... use a double boiler or something. :-)
Okay, so we've got this heated pot of scrap polymer. After a while the bits melt into a big puddle, the polymer slumps down (very slowly given its viscosity) . Now suppose we've drilled a hole in the side of the pot way down at the bottom well under the level of the molten polymer.
Then we start plumbing up a two stroke pump using Adrian's favourite plumbing parts. :-)
Here's roughly what the intake stroke looks like...

Pardon the illustration. I drew it on my white board and photographed it. That's not a great presentation method, but I'm in a hurry.
Your pot's on the left and the piston of your pump is driven by a gear motor that runs a threaded rod arrangement. I didn't get too specific on how that all fits together. At this point what is relevant is that we have what amounts to a linear motor that can deliver a LOT of thrust.
You can see two spring loaded back pressure valves. On the intake stroke the valve to the pot opens up letting the polymer melt be drawn in as the piston is pulled upwards in the cylinder.
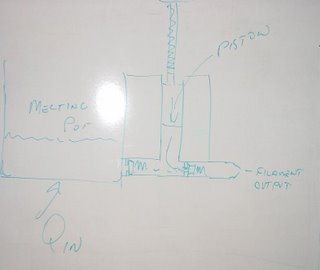
Once your cylinder is full you reverse the rotation of the gear motor which closes the back pressure valve into the pot and opens the valve to the extruder tip.
That's basically it.
What's nice is that this system can operate VERY slowly to take into account the high viscosity of the polymer melt. It can also extrude specific amounts of polymer with a high degree of accuracy. Knowing the mass flow rate of polymer out of the extruder on a real-time basis lets us control a conveyer that takes the extruded polymer away.
That's my first cut at a filament extruder.
- It can deal with either scrap polymer or virgin resin.
- It is highly controllable and information rich thereby
- It can largely be made of plumbing parts if we wish
Comments:
<< Home
I have to agree ont he complexity part. I'm familiar with concrete pumps, which are not as far removed from pumping plastics as you might think. In short, the valves will not close reliably. You need a swash plate.
I would like to speak in favour of a minimalist approach: use a screw thread to move a piston inside a tube of hot polymer - a giant icing syringe. Put the whole thing inside a block of thermal mass, bake in an oven, hook up to your motive power, then extrude. Refil, put back in oven, repeat. For higher throughput, put more than one in the oven.
I thought of making the syringe from threaded pipe and end caps. Use tank washers to hold the thermal mass in place - even concrete would do.
Joining filament is not as hard as I thought it would be. I just push heated ends into opposite sides of a 3mm hole in a PTFE block.
Vik :v)
I would like to speak in favour of a minimalist approach: use a screw thread to move a piston inside a tube of hot polymer - a giant icing syringe. Put the whole thing inside a block of thermal mass, bake in an oven, hook up to your motive power, then extrude. Refil, put back in oven, repeat. For higher throughput, put more than one in the oven.
I thought of making the syringe from threaded pipe and end caps. Use tank washers to hold the thermal mass in place - even concrete would do.
Joining filament is not as hard as I thought it would be. I just push heated ends into opposite sides of a 3mm hole in a PTFE block.
Vik :v)
I would really like it if we could use granular polymer in the RepRap write head itself and eliminate this secondary step. But the problem with that seems to be getting the mass down to a point where it can be moved. Vik's design doesn't need this at the moment, but for any machine that swaps heads and moves them about low weight is a must.
I agree on using compressed air in the chamber to create the extrusion force - that ought to work more simply than a piston.
I agree on using compressed air in the chamber to create the extrusion force - that ought to work more simply than a piston.
You'd waste a colossal amount of energy heating up such a massive chunk of hardware, though if you were mass producing colossal reels of filament then I suppose it might be worthwhile.
However, I would suggest that the one-shot pump (where you'd remove the piston and refill the chamber with granules after each cycle) might be made more time-efficient by simply fitting it with multiple nozzles, so one pressing makes lots of filaments at once. Plus, they'd all hopefully be roughly the same length - perhaps the melt head could be fed by a magazine of short rods, rather than one long filament coming from a reel. Just a thought.
However, I would suggest that the one-shot pump (where you'd remove the piston and refill the chamber with granules after each cycle) might be made more time-efficient by simply fitting it with multiple nozzles, so one pressing makes lots of filaments at once. Plus, they'd all hopefully be roughly the same length - perhaps the melt head could be fed by a magazine of short rods, rather than one long filament coming from a reel. Just a thought.
What I conceived wasn't all that massive. I had in mind that the swept volume of the polymer pump wouldn't exceed more that 4-5 cm^3. One of the earlier comments about a model airplane engine sort of fits what I had in mind insofar as scale is concerned.
At that scale one stroke would produce 500-700 mm of filament. I figure that it would be running VERY slowly since given the very high viscosity of polymer melt it would take quite a while for the dimple that filling the pump cylinder created in the pot of melt to fill in from gravitational force alone.
At that scale one stroke would produce 500-700 mm of filament. I figure that it would be running VERY slowly since given the very high viscosity of polymer melt it would take quite a while for the dimple that filling the pump cylinder created in the pot of melt to fill in from gravitational force alone.
Now THAT is a very interesting concept. It would certainly go a long way towards getting the air spaces out from between the granules and, if you used that large piston repeatedly, get rid of the dimple that extracting polymer melt from the pot would cause.
Two pistons... hmmm.. I like it!
Two pistons... hmmm.. I like it!
//just assume that we can do it without scorching.... use a double boiler or something//
How about a crock pot?
How about a crock pot?
Nice idea, but I've a feeling it'd be a real pain building an airtight port for refilling the hopper. You'd also have to ensure there was always a layer of molten material completely covering the exit hole from the pot, otherwise the air would just bypass the material and you'd end up blowing bubbles out of the extruder head!
I think, overall, I perfer the idea of having a 'spool of feed stock'... Two seperate machines, one that does the protoyping, one that creates the spools of feed stock...
You've got to store the material in some form, I think a spool of feed stock would store best (easier than pellets, powder or un/partialy recycled pieces...)
I would expect that a 'spooler' would extrude quicker than the prototyper (especially if we're talking something like 3mm vs .5mm), and could be built bigger/with a bigger capacity. This would equate to less manhours babysitting the machine... You could simply hook a spool up to the prototyper and let it run the spool dry... (big work surface, lots of items, maybe even a conveyor belt system to move away the completed parts or something)
From what I gather, it should be pretty easy to streamline a process of connecting the 'runs' to the existing spool, so long as the material is flexible enough you shouldn't have any problem spooling it up...
All in all, I think the spool is the best bet for 'continous runs'... Using sticks or a syringe or a pressurized vessel will inevitably limit the amount of material you can have 'ready' for the machine to use up... However 'big' you make it, that's the limit... With a spool system, you can just spin a bigger spool... make it wider, spin it more times... you could store all your CAPA (or whatever) on a single spool... you could have a different spool for different material/etc...
Post a Comment
You've got to store the material in some form, I think a spool of feed stock would store best (easier than pellets, powder or un/partialy recycled pieces...)
I would expect that a 'spooler' would extrude quicker than the prototyper (especially if we're talking something like 3mm vs .5mm), and could be built bigger/with a bigger capacity. This would equate to less manhours babysitting the machine... You could simply hook a spool up to the prototyper and let it run the spool dry... (big work surface, lots of items, maybe even a conveyor belt system to move away the completed parts or something)
From what I gather, it should be pretty easy to streamline a process of connecting the 'runs' to the existing spool, so long as the material is flexible enough you shouldn't have any problem spooling it up...
All in all, I think the spool is the best bet for 'continous runs'... Using sticks or a syringe or a pressurized vessel will inevitably limit the amount of material you can have 'ready' for the machine to use up... However 'big' you make it, that's the limit... With a spool system, you can just spin a bigger spool... make it wider, spin it more times... you could store all your CAPA (or whatever) on a single spool... you could have a different spool for different material/etc...
<< Home