Saturday, June 17, 2006
Testing assumptions about polymer melts...
The first assumption that I tested vis a vis the proposed filament method was whether I could melt polymer bits in a pot.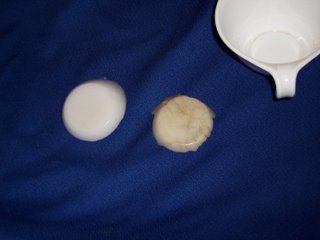
The short answer is that you can, if you put the pot in an oven where it gets heated evenly. The leftmost sample is caprolactone whilst the right is HDPE. The HDPE sample was brownish because the bits used in the melt were cut with a rusty saw. It makes for a nice marbled appearance. The caprolactone was heated for 30 minutes at 130 degrees Celsius while the HDPE was also heated for 30 minutes but at 160 degrees.
The corelle ware cup at the top right was the crucible for the melts. Corelle ware has the advantage that plastics no not adhere to it.
While I was at Santa Barbara yesterday and today I asked myself whether if you simply powered a capillary viscometer instead of putting a weighted piston on top of the polymer melt if you couldn't efficiently make filament.
The numbers seem to work. A polymer melt can easily be done in a cylinder with internal dimensions of 50 mm diameter x 100 mm height. That much melt, converted to filament, would let the Mk II operate for about 70 hours at 4 mm/sec.
I am going to go look at plumbing and piping parts this weekend and cobble something together. :-)
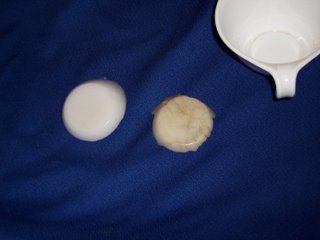
The short answer is that you can, if you put the pot in an oven where it gets heated evenly. The leftmost sample is caprolactone whilst the right is HDPE. The HDPE sample was brownish because the bits used in the melt were cut with a rusty saw. It makes for a nice marbled appearance. The caprolactone was heated for 30 minutes at 130 degrees Celsius while the HDPE was also heated for 30 minutes but at 160 degrees.
The corelle ware cup at the top right was the crucible for the melts. Corelle ware has the advantage that plastics no not adhere to it.
While I was at Santa Barbara yesterday and today I asked myself whether if you simply powered a capillary viscometer instead of putting a weighted piston on top of the polymer melt if you couldn't efficiently make filament.
The numbers seem to work. A polymer melt can easily be done in a cylinder with internal dimensions of 50 mm diameter x 100 mm height. That much melt, converted to filament, would let the Mk II operate for about 70 hours at 4 mm/sec.
I am going to go look at plumbing and piping parts this weekend and cobble something together. :-)
Comments:
<< Home
One common way to degas a viscous liquid is to pull a vacuum on it several times. This might also help to pull additives/free monomers out of the plastic, if they're volatile, and could even help keep the PET from being degraded. Does anyone have a setup that would allow them to pull the air out of their crucible? It could even be a hand pump, since really low pressure isn't necessary.
Post a Comment
<< Home