Wednesday, June 21, 2006
Shopping...
The new PIC programmer is on order and should be here by Thursday or Friday. Randy at Glitchbuster is just over the state line in Nevada right by Lake Tahoe.
In the meantime I put all the Mk II parts in a ziplock and headed down to the hardware supply store.
The M3 bolts aren't readily available in the lengths that Adrian specified, nor is M5 studding.
I was able to match M3 bolts pretty closely with American machine bolts size 10-40 and while 1/4-inch American studding is a bit bigger than M5 (a bit of widening of the cavity will be required) the pitch of the threads is virtually identical (20/inch = 0.79 metric pitch while M5 has 0.8 pitch).
Here's the Americanised Mk II bolted together...
I decided to simply size up my piston extruder concept. I hit the plumbing section of the hardware store and discovered that steel pipe is welded seam and the seams are NASTY, so I went for brass.
I tapped the cap with the same 7/64-inch drill bit that produced 3.15 mm diameter filament in earlier experiments. Interestingly, the cap thickness is no more than 2 mm.
I will be buying a few 16F877A's for running the Mk II so that I don't have to be so clever in measuring things like thermistors and Hall-effect chips.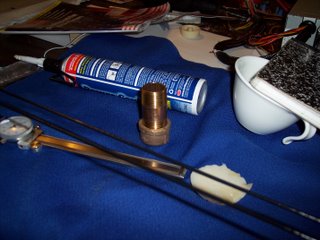
I'm planning on making a piston out of the ubiquitous poplar and also make a poplar bracing rack for it in the toaster oven with a bamboo plug for the extrusion orifice. This one is a 22 mm diameter x 52 mm. It holds 19.3 cm^3 of polymer which is enough for 2.7 metres of filament which will keep the Mk II going for a bit over 2 hours and 30 minutes at 4 mm/sec.
Basically, you fill it with polymer pellets, pop it in the toaster oven and when it's ready take it out and extrude filament.
This one I plan to run by hand again and, if I get promising results, attach to the Siemens gearmotor to it using the thrust design that Brett put together some months ago.
In the meantime I put all the Mk II parts in a ziplock and headed down to the hardware supply store.
The M3 bolts aren't readily available in the lengths that Adrian specified, nor is M5 studding.
I was able to match M3 bolts pretty closely with American machine bolts size 10-40 and while 1/4-inch American studding is a bit bigger than M5 (a bit of widening of the cavity will be required) the pitch of the threads is virtually identical (20/inch = 0.79 metric pitch while M5 has 0.8 pitch).
Here's the Americanised Mk II bolted together...

I decided to simply size up my piston extruder concept. I hit the plumbing section of the hardware store and discovered that steel pipe is welded seam and the seams are NASTY, so I went for brass.
I tapped the cap with the same 7/64-inch drill bit that produced 3.15 mm diameter filament in earlier experiments. Interestingly, the cap thickness is no more than 2 mm.
I will be buying a few 16F877A's for running the Mk II so that I don't have to be so clever in measuring things like thermistors and Hall-effect chips.
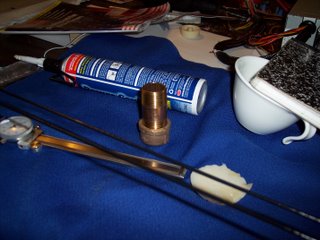
I'm planning on making a piston out of the ubiquitous poplar and also make a poplar bracing rack for it in the toaster oven with a bamboo plug for the extrusion orifice. This one is a 22 mm diameter x 52 mm. It holds 19.3 cm^3 of polymer which is enough for 2.7 metres of filament which will keep the Mk II going for a bit over 2 hours and 30 minutes at 4 mm/sec.
Basically, you fill it with polymer pellets, pop it in the toaster oven and when it's ready take it out and extrude filament.
This one I plan to run by hand again and, if I get promising results, attach to the Siemens gearmotor to it using the thrust design that Brett put together some months ago.
Comments:
<< Home
So what are you thinking of using to catch the melted 3mm plastic rod?
Been wondering what the best method is for getting the 3mm rod to stay nice and rounded after it leaves the melt chamber. I think it was Adrian who extruded it into a bucket of water...?
Been wondering what the best method is for getting the 3mm rod to stay nice and rounded after it leaves the melt chamber. I think it was Adrian who extruded it into a bucket of water...?
I originally extruded filament into water. With the piston extruder, however, I've been able to extrude caprolactone at about 95 degrees Celsius. At that temperature you don't get a lot of distortion. I catch it on a cookie sheet. :-D
For now, I'll have my son pull the filamentand spool it. I'll work out something more formal after I've extruded at a few different swept volume sizes.
Post a Comment
For now, I'll have my son pull the filamentand spool it. I'll work out something more formal after I've extruded at a few different swept volume sizes.
<< Home