Thursday, March 23, 2006
A workable coupling for the filament extruder
A visit to the local hardware store yielded a short length of 3/8-inch (9.5 mm) ID 200 psi (13.4 atm) test air hose.
That provided a perfect friction fit for the 10.4 mm bit shank and the extender for the electric drill. I didn't even have to use the hose clamps that I had bought to go with it. This joint didn't slip under any circumstances.
I set up to do a filament extrusion test with a 58-60 Celsius quenching bath. Unfortunately, I'd neglected to put a full charge on the electric drill, so it ran much slower than usual which meant that I had a very uneven extrusion rate. All the same, the filament production even under these adverse circumstances was quite good.
This time I teased the filament out into straight sections with a bamboo stick. In the pic the calipers are opened to 100 mm for scale.
I got an irregular extrusion rate that meant that diameter control wasn't so good this time. Tomorrow I will try it again with a full battery charge and see what happens. If that's good I'll start looking at some marble dust filler mixes to see what goes on with extruding filled polymer.
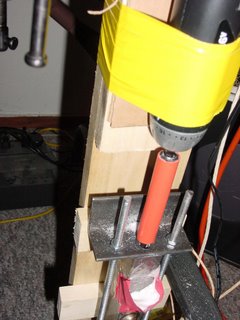
I set up to do a filament extrusion test with a 58-60 Celsius quenching bath. Unfortunately, I'd neglected to put a full charge on the electric drill, so it ran much slower than usual which meant that I had a very uneven extrusion rate. All the same, the filament production even under these adverse circumstances was quite good.
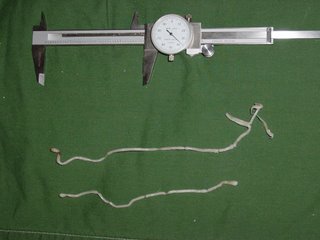
I got an irregular extrusion rate that meant that diameter control wasn't so good this time. Tomorrow I will try it again with a full battery charge and see what happens. If that's good I'll start looking at some marble dust filler mixes to see what goes on with extruding filled polymer.