Friday, January 27, 2006
Steppers vs. Servos
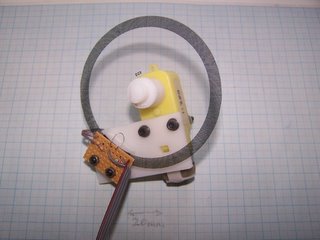
At the RepRap project we have a never-ending discussion about the relative merits of stepper motors (simple, implicitly digital, but low torque and expensive) and DC motors (more complicated to control, but high-torque and cheap). This small discussion mirrors a much larger one that has been going on for years in the machine tool and robotics industries. It hasn't been resolved there, so we probably won't arrive at a definitive answer either.
To start with, RepRap will most likely use steppers, as we don't need a lot of torque (additive manufacturing is inherently very low force) and their simplicity of control cuts down on electronics - a big bonus.However, I though I'd see if I could make a very cheap and simple DC digital servomotor using rapid prototyping. It's depicted above. I've put preliminary details on the RepRap Wiki.
Comments:
<< Home
Mark's point about absolute encoding is well-made. But we will probably have separate axis-zero detectors anyway (keyed on the write heads, so registration is automatic). Gray code would be good, but needs more detectors, of course.
Laserprinters certainly make darker patterns than inkjets - I have used laserprinted acetate sheets for UV masks for PCB production; you can't do this with an inkjet. But inkjets are a lot more widespread and cheaper - something that RepRap will benefit from.
Laserprinters certainly make darker patterns than inkjets - I have used laserprinted acetate sheets for UV masks for PCB production; you can't do this with an inkjet. But inkjets are a lot more widespread and cheaper - something that RepRap will benefit from.
Yes - the machine could make the pattern and, as it evolves, it will certainly become more accurate than inkjet printers.
There are problems with the growth of errors, but they can be minimised by making a map: you make a not-very-good wheel and use it to lay down (say) a comb shape with nominally 1mm teeth. Then you measure them accurately and use the measurements to correct for the mistakes in the wheel.
There are problems with the growth of errors, but they can be minimised by making a map: you make a not-very-good wheel and use it to lay down (say) a comb shape with nominally 1mm teeth. Then you measure them accurately and use the measurements to correct for the mistakes in the wheel.
I look at this and I think: Turntable!
400 steps is a bit light on resolution, but might be good for rotationally symetric objects like gears and so forth. I could maybe treble the resolution with an anti-backlash gear. So much to design, so little time...
I have a 4096-step magnetic rotary encoder module if you'd like it, Adrian.
Vik :v)
400 steps is a bit light on resolution, but might be good for rotationally symetric objects like gears and so forth. I could maybe treble the resolution with an anti-backlash gear. So much to design, so little time...
I have a 4096-step magnetic rotary encoder module if you'd like it, Adrian.
Vik :v)
Funny you should mention turntable, Vik. A few days ago I was buying parts for godzilla in a large hardware store and found a lazy suzan turntable with a loaded ball bearing raceway. Very smooth action. 300 mm diameter US$7.99.
So many things that can be put to very different uses... so little time to shop. :-(
So many things that can be put to very different uses... so little time to shop. :-(
4096!!! Wow - is it commercially available, and if so is it expensive? At that resolution I would expect it to be a bit special in the finance department...
Post a Comment
<< Home