Wednesday, December 14, 2005
Building the filament extruder version 1.0
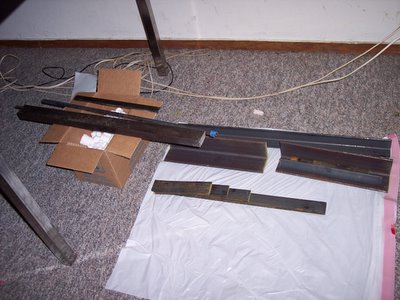

We collected the steel for the extruder too late to do anything with it yesterday. This morning I acquired a small mitre box and some fresh hacksaw blades and spent the rest of the day cutting the big chunks of steel bar and angles into smaller ones as per the design specifications. Tomorrow, after cutting the few remaining bits save the extruder block, I will round off the edges and corners with a grinder and, with a bit of luck, drill the holes for the bolts used to put it all together.
I also discovered that you do most definitely not put steel fresh from the steel yard onto a carpet.
Comments:
<< Home
For cutting steel in a hurry, I really, really recommend an angle grinder, gloves and eye protection. Use cutting discs 1-2mm (0.07-0.04 inch) thick, and they'll just slice through. With grinders on special at NZ$10 these days, they're dead cheap and really handy to have around.
Of course, it makes a noise like a jet at takeoff, and fires sparks across the yard, but what the hey :)
Vik :v)
Of course, it makes a noise like a jet at takeoff, and fires sparks across the yard, but what the hey :)
Vik :v)
I wasn't in a hurry and am trying to avoid lumbering myself with a bunch of tools that I really can't justify buying. If I had a big workshop it might be another matter, but I don't, currently.
As it is, I did the majority of the cutting work with a hacksaw I borrowed from my brother-in-law and a $4.99 mitre box in about a day.
As it is, I did the majority of the cutting work with a hacksaw I borrowed from my brother-in-law and a $4.99 mitre box in about a day.
Ah, I see. I bought mine because I am restoring a fire engine (1943 Ford "Jailbar") - but you'd be surprised how often I use it now I've got it.
Maybe one day we'll be able to RepRap ourselves new ones :)
A RepRap'd lathe just has to happen...
Vik :v)
Maybe one day we'll be able to RepRap ourselves new ones :)
A RepRap'd lathe just has to happen...
Vik :v)
First you learn to cast metal...
http://www.backyardmetalcasting.com/index.html
...then you make your lathe.
http://www.backyardmetalcasting.com/lathe1.html
...then, of course, you will want a milling machine, a shaper, a drill press... and so on and so on.
http://www.lindsaybks.com/dgjp/djgbk/series/index.html
With RepRap you could make the patterns for metal casting a lot more easily than hand carving them out of wood.
http://www.backyardmetalcasting.com/index.html
...then you make your lathe.
http://www.backyardmetalcasting.com/lathe1.html
...then, of course, you will want a milling machine, a shaper, a drill press... and so on and so on.
http://www.lindsaybks.com/dgjp/djgbk/series/index.html
With RepRap you could make the patterns for metal casting a lot more easily than hand carving them out of wood.
When you first mentioned making a metal lathe of polymer the idea struck me as daft, which is why I suggested using the reprapped bits as molds for metal casting. The more I think about it, though, the more reasonable it sounds.
It certainly wouldn't have the same dimensions as a metal lathe made of metal because of the much lower yield strength of the polymer and its tendency to creep.
It's a fascinating idea.
Post a Comment
It certainly wouldn't have the same dimensions as a metal lathe made of metal because of the much lower yield strength of the polymer and its tendency to creep.
It's a fascinating idea.
<< Home