Saturday, January 10, 2009
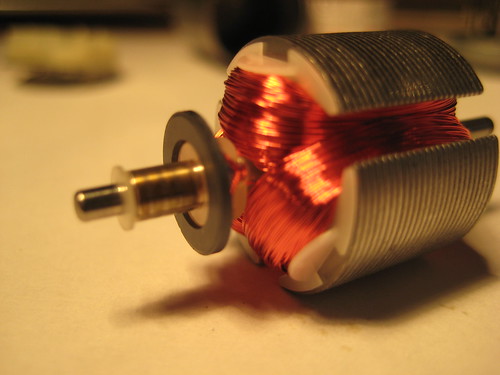
We've been using GM3 gearmotors for our RepRap extruder motors, but they have a few problems (most notably being underpowered and having cheap plastic gears) so I decided to shop around and try to find a motor that I could be proud of. I stumbled onto the site kysanelectronics.com and ordered a bunch of their 12v DC gear motors. I got about 10 different motors with various gear ratios, sizes, etc. I decided to sacrifice one and take it apart. Turns out I was actually (miraculously?) able to piece it back together again, in working order too!
Here is a flickr set with the teardown.
Anyway, here are a few observations about these motors:
* they are all-metal construction (gears, housing, shafts, etc) the only plastic was an insulator on the terminals
* they are very powerful (my test is attaching vice grips and letting them rotate the vice grips, then trying to stop the rotating pliers with my hands. all could easily move the pliers, and most took a decent amount of force to stop)
* they are pretty cheap! for a single motor, they are $9.07 for a single unit and at volumes of 100+ they drop to $7.34. Not as cheap as the GM3, but they have dramatically higher strength, etc.
I think I may just have to place an order for a hundred of them. =)
Comments:
<< Home
It is the brushes that wear out first on the GM3, not the plastic gears.
The 6V GM3 had thin brushes like this motor and they did not last for long at all. The 12V version has much thicker metal brushes but still nowhere near the life required.
I don't think a DC motor running continuously is going to cut it. Certainly not a toy grade one, a proper industrial one with carbon brushes perhaps.
By the time you have added the cost of a shaft encoder and suppressor and then replaced the motor a few times it ends up cheaper and simpler to use a stepper.
The 6V GM3 had thin brushes like this motor and they did not last for long at all. The 12V version has much thicker metal brushes but still nowhere near the life required.
I don't think a DC motor running continuously is going to cut it. Certainly not a toy grade one, a proper industrial one with carbon brushes perhaps.
By the time you have added the cost of a shaft encoder and suppressor and then replaced the motor a few times it ends up cheaper and simpler to use a stepper.
If you want a more industrial dc gear motor try Anaheim Automation (http://www.anaheimautomation.com/brush-dc-planetary-gearmotor-bdpg-38-86.aspx). I like this series the best for RepRap. The price is a little higher, ~$37, but if you are going to get a lot better performance. If you do want to have a real servo with encoder feed back you should really use a motor that will be worth it. By the way, the Anaheim motors could probably drive the filament directly with a "worm gear" design like aka47 is working on. Just mount the worm gear right on the shaft of the motor. Boy could that simplify the extruder :) But hey, the kysan motors you found could do the same, it is hard to tell because there aren't really any specs or drawings on the kysan site. Twice to three times the price for the motor is worth reduced overall complexity and part count in my humble opinion. I'm rambling now, but I wanted to point out the rated torque on the 30 rpm (BDPG-38-86-12V-3000-R100) motor is 416.62 oz-in. The GM 3 is rated at 50 oz-in with about the same top speed. However, the kysan B42RE191i offers similar torque at $13.00... What do the brushes and bearings look like. Some of those kysan motors come with encoders, in the $50-80 range. You can't get the Anaheim DC gear motors with a encoder installed, you have to go to the brushless motors to get an encoder on it. Ok, I have type for too long again, I'll stop right now.
Zach et al,
Thanks for the link.
Are these surplus, or not? Designing in a surplus item is risky, because the supply can vanish without warning. Metal gearing sounds nice, but I seem to recall that the motor's brushes went first. I'm going to try slot-car motors as replacements for the GM3 motor -- dual shafts (thus one for an encoder) and (I hope) better quality brushes.
Thanks for the link.
Are these surplus, or not? Designing in a surplus item is risky, because the supply can vanish without warning. Metal gearing sounds nice, but I seem to recall that the motor's brushes went first. I'm going to try slot-car motors as replacements for the GM3 motor -- dual shafts (thus one for an encoder) and (I hope) better quality brushes.
I have had a quick look at the motors and they look remarkably similar to a bunch of motors and gear boxes supplied in the UK by MFA COMO
http://www.mfacomodrills.com/gearboxes/gearboxes.html
I was looking at some of their range some time ago.
Given their similarities and a discusion I had with on of their sales staff (I wanted the 12v versions with the shaft extended the rear so we could mount an encoder to it, and they couldn't manage this for a sensible price) I am given to understand that these items are sourced in China.
Zach if you are planning to buy in job lots it could be worth moving upstream with the purchase.
I think Forest had some contact with a Chinese motor company (for steppers) Could be worth consulting with him....
http://www.mfacomodrills.com/gearboxes/gearboxes.html
I was looking at some of their range some time ago.
Given their similarities and a discusion I had with on of their sales staff (I wanted the 12v versions with the shaft extended the rear so we could mount an encoder to it, and they couldn't manage this for a sensible price) I am given to understand that these items are sourced in China.
Zach if you are planning to buy in job lots it could be worth moving upstream with the purchase.
I think Forest had some contact with a Chinese motor company (for steppers) Could be worth consulting with him....
aka47: I think Forest had some contact with a Chinese motor company (for steppers) Could be worth consulting with him....
Naah, Zach already went that route. The shipping was prohibitive even though the price was attractive that Zach got really burned. I don't think that he ever used the ones that he got from that shipping intense order. Poor Annie in Shanghai was crushed, iirc.
Naah, Zach already went that route. The shipping was prohibitive even though the price was attractive that Zach got really burned. I don't think that he ever used the ones that he got from that shipping intense order. Poor Annie in Shanghai was crushed, iirc.
larry: no, these are not surplus. i pretty much only buy stuff that i can get repeat buys of. i specifically asked if it would be possible to get 1000 of the motor and they said yes.
everyone else: thanks for the input! now that i've used these motors, i'm really loving them (i'll post a blog entry on that later) but i also have some additional sources lined up should these fail too soon.
everyone else: thanks for the input! now that i've used these motors, i'm really loving them (i'll post a blog entry on that later) but i also have some additional sources lined up should these fail too soon.
I feel like this might be a move in the wrong driection. Every choice we make should be motivated by the thought that we'll eventually want to be able to print all of the parts. Using a GM3 motor with weaker plastic gears constrains us to think of extruder designs that don't require as much torque. Therefore, in the future when we are printing the gears with the machine, we will have an extruder design that is compatible with the plastic gears. Using a beefier, all-metal motor now could guide the extruder's evolutionary path toward a more wasteful, less elegant design that will be ultimately incompatible with the overall project objectives. What do you think?
Do you want the machine to work better and be more reliable or do you want it to be able to replicate more of its own parts, even those that are easy and not too expensive to buy?
to nophead:
I want both. Each ultimately propels the RepRap project forward. More RP'd parts make the movement more unique (it's not just another rapid prototyping project), and more affordable. If the project was at 100% RP'd part status, the whole machine would cost a couple bucks in plastic, further encouraging people to get involved, and ever increasing the rate of machine improvements.
I look at it this way: Sometimes there are multiple solutions to a problem, and one of them might be compatible with both objectives. In the case of the extruder motor: If friction in the design is greater than a motor's torque can overcome there are two options: increase the motor's torque or decrease the friction. The latter, if not to difficult to implement, might be the better option.
I want both. Each ultimately propels the RepRap project forward. More RP'd parts make the movement more unique (it's not just another rapid prototyping project), and more affordable. If the project was at 100% RP'd part status, the whole machine would cost a couple bucks in plastic, further encouraging people to get involved, and ever increasing the rate of machine improvements.
I look at it this way: Sometimes there are multiple solutions to a problem, and one of them might be compatible with both objectives. In the case of the extruder motor: If friction in the design is greater than a motor's torque can overcome there are two options: increase the motor's torque or decrease the friction. The latter, if not to difficult to implement, might be the better option.
nophead:
A good example might be Zach's pinch wheel extruder. I wonder if that design has less inherent friction?
Post a Comment
A good example might be Zach's pinch wheel extruder. I wonder if that design has less inherent friction?
<< Home