Tuesday, March 28, 2006
Serendepity strikes again...
Hey! I'm not claiming to have "invented" any of this, okay? I've been through the archives and I see that Adrian and Vik, I think, did all this on a smaller scale a long, long time ago. Indeed, I originally set out to make a Gingery piston extruder which uses the same principle.
Anyhow, here goes. I had to drill out the extruder barrel to get the marble dust/CAPA mix clear of it this morning. It was quite a mess to say the least. This afternoon I thought about running that mix through the polymer pump again and sort of wilted at the thought. I thought about those push filament through with your hand experiments in the archive. I took the cleaned extruder barrel, insulated it with two scraps of poplar wood, filled it up with the marble dust/CAPA mix and kicked on the cartridge heater. In 2-3 minutes the IR thermometer said that it was nearing 100 degrees Celsius, so I inserted a .25-inch rod into the barrel and gave the charge a tentative push. I estimated that I applied about 10 lbs of thrust which put the cartridge barrel at about 14-15 atm. I emptied the barrel in about 5-10 seconds of steady pushing.
I got a 300 mm long filament out of that which was a uniform 3.175 mm in diameter. Because of the lower temperature and possibly the filler the filament was self-supporting. I caught the filament in a cup of cold water. Here it is. The colour is nasty because I didn't finish the drillout with an alcohol swabbing.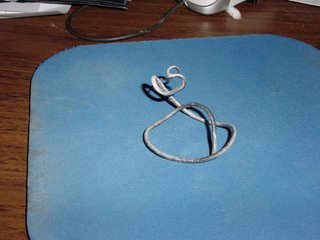
The filament was straight coming out but got bent and twisted in the small cup of water.
What I did here reminds me more than a little of Adrian's bicycle pump filament maker idea. The filament that resulted is quite flexible and more than a little like Weedeater cord in feel.
This mix is 40% calcium carbonate by volume and roughly 60% calcium carbonate by weight.
If this mix produced a usuable filament in the Mk II it would bring the cost of extrusions down from US$12.73/kg to US$8.52/kg. I suspect that if we bought marble dust in 20 kg sacks like we will the CAPA that our mix price would drop to somewhere in the vicinity of US$7.73/kg.
The quality of the filament and the ease and speed of it's manufacture has got me to thinking about the notion of a reciprocating piston extruder again. Brett brought up something like that in a discussion we had some weeks ago. Hmmm...
LOL! :-)
Anyhow, here goes. I had to drill out the extruder barrel to get the marble dust/CAPA mix clear of it this morning. It was quite a mess to say the least. This afternoon I thought about running that mix through the polymer pump again and sort of wilted at the thought. I thought about those push filament through with your hand experiments in the archive. I took the cleaned extruder barrel, insulated it with two scraps of poplar wood, filled it up with the marble dust/CAPA mix and kicked on the cartridge heater. In 2-3 minutes the IR thermometer said that it was nearing 100 degrees Celsius, so I inserted a .25-inch rod into the barrel and gave the charge a tentative push. I estimated that I applied about 10 lbs of thrust which put the cartridge barrel at about 14-15 atm. I emptied the barrel in about 5-10 seconds of steady pushing.
I got a 300 mm long filament out of that which was a uniform 3.175 mm in diameter. Because of the lower temperature and possibly the filler the filament was self-supporting. I caught the filament in a cup of cold water. Here it is. The colour is nasty because I didn't finish the drillout with an alcohol swabbing.
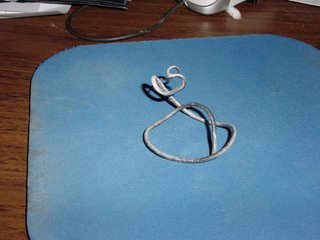
The filament was straight coming out but got bent and twisted in the small cup of water.
What I did here reminds me more than a little of Adrian's bicycle pump filament maker idea. The filament that resulted is quite flexible and more than a little like Weedeater cord in feel.
This mix is 40% calcium carbonate by volume and roughly 60% calcium carbonate by weight.
If this mix produced a usuable filament in the Mk II it would bring the cost of extrusions down from US$12.73/kg to US$8.52/kg. I suspect that if we bought marble dust in 20 kg sacks like we will the CAPA that our mix price would drop to somewhere in the vicinity of US$7.73/kg.
The quality of the filament and the ease and speed of it's manufacture has got me to thinking about the notion of a reciprocating piston extruder again. Brett brought up something like that in a discussion we had some weeks ago. Hmmm...
LOL! :-)
Comments:
<< Home
I know a little about piston-based extruders, as I worked for a concrete pump company called AFD many, many years ago. I think they've gone under now, but here's basically the thing we used to make:
http://www.auscrete.com.au/piston_pump_design.htm
But it looks like the extrusion you're doing manually is shaping up very well.
Vik :v)
http://www.auscrete.com.au/piston_pump_design.htm
But it looks like the extrusion you're doing manually is shaping up very well.
Vik :v)
Have you thought about using aluminum silicate powder instead? It's even cheaper than marble powder, easier to manufacture and more chemically stable (no reaction with acids, a big problem with CaCO2) I've got about a million and a half tons of the stuff in my front yard (AlSiO2 is also called "clay" )
Kaolin is probably the form of clay we'd use and your points are well-taken about price and reactivity.
I know that calcium carbonate used as a filler tends to make the mix easier to extrude. I'm not sure what the effect of using kaolin would be. The reference I found about it talked only about improvements of processability.
http://media.wiley.com/product_data/excerpt/41/35273105/3527310541.pdf
Post a Comment
I know that calcium carbonate used as a filler tends to make the mix easier to extrude. I'm not sure what the effect of using kaolin would be. The reference I found about it talked only about improvements of processability.
http://media.wiley.com/product_data/excerpt/41/35273105/3527310541.pdf
<< Home