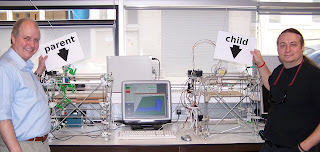
Adrian (left) and Vik (right) with a parent RepRap machine, made on a conventional rapid prototyper, and the first complete working child RepRap machine, made by the RepRap on the left. The child machine made its first successful grandchild part at 14:00 hours UTC on 29 May 2008 at Bath University in the UK, a few minutes after it was assembled.
[Sorry this news is a few days late, RepRap fans. We had a press embargo on it till 4 June to coincide with the opening of the Cheltenham Festival (see above and below), and it wouldn't be very good practice to break our own embargo :-)]
Congratulations! I assume you will be wetting the babies head now!
ReplyDeleteWell done chaps!!
ReplyDelete'from strength to strength'
[m]
Good going!
ReplyDeleteSo, does this mean we'll see cheap/affordable repraps on the market this year, then? ;)
So, is the child considered generation 1 or 2?
ReplyDeleteAwesome! And congrats!
ReplyDeleteI assume this is just the brackets and plastic parts, right? Or can it literally do the entire thing, modulo maybe a few screws and wires?
Great pic, guys! :-D
ReplyDeleteI couldn't help but notice that the child uses ball chain, not belts. Glad to see that's working OK.
ReplyDeleteCongratulations!
ReplyDelete(Maybe you can get yourselves slashdotted again!)
Congratulations!
ReplyDeleteWe need a numbering scheme: eg 1 (the first machine to self-replicate) 1.1 (the first child of the first machine), 1.2 (the second child of the first machine), 4.3.6.1 (the first child of the sixth child of the third child of the fourth RepStrap machine to achieve self-replication).
This would elegantly provide a unique number for every machine ever produced.
Congrats to all of you! Keep on rocking.
ReplyDeleteI'm sure you'll find a use for those exponentially proliferating shotglasses:-)
ReplyDeleteGreat picture!
ReplyDeleteI see the flex drive is not used and the ball chains. I think it is safe to say that the flex drive is a 'fragile' part. The ball chain is easier to get, so that's also an improvement.
I like Steve Baker's numbering scheme. It is both elegant and descriptive.
Congratulations! Well done!
ReplyDeleteVinay Gupta
http://globalswadeshi.org
Congrats on this achievement! One step closer to true VNB! :)
ReplyDeleteSmári, Fab Lab Iceland.
I updated the Wikipedia RepRap article to include some of the recent advances. Would it be possible to release the photo attached to this thread with a GFDL or CreativeCommons license so it could be used to illustrate the Wikipedia article?
ReplyDeleteThanks everyone! And not just for your congratulations - you have contributed both work and ideas without which we all would never have got here.
ReplyDeleteYes - I too like Steve's numbering scheme. Now we just have to remember to keep track...
The picture is covered by the GPL, like every other byte on the RepRap site. So do with it whatever you like.
Congrats!
ReplyDeleteCongrats...awesome. This is an event to remember. You all deserve a great pile of gratitude for all the hard work...I'm still in awe.
ReplyDeleteVery cool, congratulations! And following right on the heels of nophead's beautiful door handle, it's a great week for RepRap.
ReplyDeleteWell done!!!
ReplyDeleteCan't wait to see repraps all around the place!
Please add my congratulations as well.
ReplyDeleteDo we have a latin name and appropriate taxonomy for it yet ??
ReplyDeleteWe need something to chart the evolution <|;)
Its not a number it's a machine. (Although a number is good too)
Grin
aka47
sounds great, but what about all of those microcontrollers?
ReplyDeleteDo you mean its have been replicated with the RepRap itself?
Congratulations on your success here, but could you give some more details on exactly what the milestone is? Is this 100% replication given a list of base parts including microcontrollers and motors?
ReplyDeleteI for one, welcome our new self-replicating overlords..
ReplyDeleteSo it doesn't make the motors or the metal rods, just the little plastic bits. Nor does it assemble the parts. That doesn't seem very self-replicating to me.
ReplyDeleteIt's a bit like using a photocopier to copy its manual.
That doesn't seem very self-replicating to me. It's a bit like using a photocopier to copy its manual.
ReplyDeleteNot really. The photocopier is not making parts for daughter photocopiers.
A better analogy would be to say it's like using a CNC lathe to make another CNC lathe. You still need some other way to make the gears, and many other parts, like the motors and the circuit boards, to say nothing of having to cut down large stock to useful size, but the finished machine is still useful.
Fussing that RepRap is not perfect yet is an extremely common criticism which glosses over the fact that it's a machine that cheaply and easily makes its own parts*, using inexpensive feedstock. And it can make other useful things. That's the important stuff, which your criticism fails to address.
*Aside from common stuff from a hardware store and an electronics store.
Just for the record, the Child was made with a RepRap of the same design as Adrian's, not actually with it. My family withstood many hours of strange mechanical and swearing noises, and deserve some recognition also!
ReplyDeleteVik :v)
Very cool, keep it up!
ReplyDeletethe fist step to terminator :D
ReplyDeleteSebastien, I hope my comment didn't sound too critical, I have been a fan of reprap for a few years now and I think this is a very important work. Perhaps some of the negative comments stem from not understanding what you've defined as self-manufactured components and what are 'common parts' like motors. Some people might not be happy until it makes itself entirely from soil, but at the other extreme one could claim to have a self-replicating machine if they listed 'one reprap' as its sole component. You are obviously some way between those extremes - and getting closer to the former. Perhaps some more detail on the exact point you're at would help?
ReplyDeletesrimech, right now the RepRap can make all its own plastic parts. Next up will be printing circuit boards.
ReplyDeleteTechnically, we should distinguish between "weak" replication and "strong" replication (to invent terminology), but it's too much bother.
Normally we just say it's self-replicating, and then go on to specify what the machine is capable and incapable of doing. Even so, in every comment thread we get pedantic types like kodabar saying "Welllll, it's not realllly self replicating..." It's a tedious criticism which is very easy to make, and one which ignores the merits and drawbacks of the machine.
Merits/Drawbacks include:
{price, ease of use, self-replication, usability, open source} / {no support material yet, can't make small (1mm-2 mm) gear teeth yet (or toothed belt, threaded rod), can't do materials like metals/ceramics yet, etc.}
It might be tedious criticism from some, but others really just don't know exactly what the machine can do.
ReplyDeleteI agree with whoever said you should say what exactly it is making. You don't need to invent terminology, just say "RepRap can make X% of its plastic parts, Y% of the metal ones and Z% of the electronics" or whatever.
"I'm going to print more printers, Lanie. Lots more printers. One for everyone."
ReplyDeleteGrats to everyone involved in RepRap. I've been watching the project for a while and waiting to hear this -- you guys are totally badass.
I agree with Du and whoever said; declare exactly what we're making. I suggest the % component mass that Darwin can make.
ReplyDeleteFor example, "RepRap can make X% of its parts by mass."
If you do a part count of the mechanics, washers swamp everything... If you leave out fastenings, then RepRap makes about 60% by count of its mechanical parts.
ReplyDeleteOf course, no one writing to this blog is a true replicator either - there are eight amino acids that none of us can make, and none of us can make vitamin C, and - well, the list is endless...
Adrian,
ReplyDeleteThat's a factually true but emotionally unconvincing position.
Fundamentally, it's arguing over definitions, when what people in both camps* should be doing is is getting off their fundaments and making more and better RepRaps.
*I'm in the "Sure it's self-replicating, you see two machines there, don't you?" camp.
Sebastian,
ReplyDeleteYou don't actually expect a critic to DO SOMETHING[!] do you? They're only programmed to make facile objections.
Congratulations (Grandpa) Adrian.
Hey, I just stumbled on RepRap today and I have to say - this is amazing! Congrats on this major milestone, and hopefully I'll get myself a RepRap of my own sometime soon.
ReplyDeleteI realize that the RepRap project is economics-challenged (e.g. "Wealth Without Money"), but perhaps self-replication should tip on cost? The RepRap self-replicates because it makes all the parts that are cheaper to make than buy.
ReplyDeleteSimilarly, it's cheaper for people to assemble the RepRap than for it to assemble itself. At some time in the future that will change, at which point somebody will make a reprap that assembles itself.
This comment has been removed by the author.
ReplyDeleteThere could be nice synergies with this. Lego bricks for some parts, reprap pieces for other parts. Funny looking hybrids we could be looking at!
ReplyDeleteUm.. doesn't anyone watch Stargate SG-1??? Can you say 'Replicators'????
ReplyDeleteScary.
:D
thank you for your breakthrough work, as a cyborg anthropologist, i am truly excited by this development.
ReplyDelete"Can you say 'Replicators'???? Scary."
ReplyDeleteI know that was a joke, but I was asked this by a journalist today. Most people who do ask it seem not to have realised that replicators are the one type of thing that humanity is most used to dealing with.
We call it agriculture.
And for the last 12,000 years agriculture has always trodden the same path: domesticated replicators are more compliant, more docile, more hard-working, and more productive than their wild cousins because that's how we breed them. RepRap starts off as a domesticated replicator.
How many people are frightened of a tulip?
I have built about 40 proto-type CNC machines and I sell plans for I think 10? I can see your machine has a seconday use if you can get it to make objects out of wax that could then be case using the lost wax method and aluminum.
ReplyDeleteJohn Cranky Kleinbauer
www.crankorgan.com
my gosh, I didn't get a chance to go online til now due to multiple assignments... major congrats!!
ReplyDeleteCranky - the lost wax and aluminum idea is one that has occurred to me as well. I've read about lost wax but never tried it. How does one melt the aluminum?
ReplyDeleteLost Wax or Foam (styrofoam) works the same way. You put the Wax or Foam model in a casting material. After the casting material dries you pour in the aluminum. The Foam or Wax is burn off or LOST!
ReplyDeleteSee link
http://www.theworkshop.ca/casting/casting.htm
1st,2nd,etc. generation replication NOT a child-
ReplyDeleteAhhh ... self replication, I guess that means you can print metal supports, circuit boards, and copper wiring ... congrats!
ReplyDeleteWhen I envision "replication", it involves the self-manufacture of 100% of the parts as well as complete assembly. They really need to quit flogging the "achieved replication" thing until they actually achieve it.
ReplyDeletedo these machines have a purpose other then self replicating??
ReplyDeleteYes they make atrbitrary 3D plastic objects from computer models.
ReplyDeleteComplexity costs nothing so, once designed, anything can be made for just the price of the plastic which is pennies.
Thank you for your fine work.
ReplyDelete-Skynet.
nice post!So, does this mean we'll see cheap/affordable repraps on the market this year, then? ;)
ReplyDelete