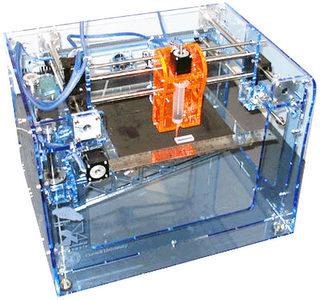
Evan Malone and Hod Lipson at Cornell have done some nice work;
They've got a syringe-based 3D printer, with full plans, up at:
http://128.253.249.235/wiki/index.php?title=Main_Page
It doesn't make copies of itself or work with thermoplastic but it's quite
impressive. The printer is made from laser cut acrylic sheet. "Approx.
$1500 RP system", according to a person who saw a talk by them.
It might be worth talking to these fellows and seeing if they would like to work together with us. I'm curious what license they're going to release his work under, what precision they're working at, and so on. They know about our project - they mention RepRap in their overview.
I think it would be extremely worthwhile to merge some of our work with
theirs, if we can sort out architectures, GPL, and so on. What do you guys think? At the very least we could use their system as a RepStrap, similar to Vik's flat-pack-RepStrap idea.
We've got 2 syringe-based systems. One for depositing liquid alloy, one for depositing cellulose filler paste.
ReplyDeleteThere is a lot of thick, expensively-cut acrylic in the Fab@home design. I'm sure we could do something that could be hacked out by routing processes in 6mm acrylic - the thickest most machines can cut with a router in one pass.
We'd have to design it so that it coped with the rounded interior cuts that routers produce, but that's not rocket science.
Oh for more time and a budget. I feel I am not alone in wanting to do this for a day job...
Vik :v)
The folks over at MIT's "Fab Lab", the Center for Bits and Atoms, http://fab.cba.mit.edu/ would also be a great group of people to get on board with. They've been setting up "Fab" shops in remote places and tackling all sorts of esoteric rapid prototyping projects. Their main man, Neil Gershenfeld, wrote a book entitled "how to make (almost) anything" and another entitled "Fab" all good reading.
ReplyDeleteI get around. It's either "community outreach" or "goofing off, surfing the web".
ReplyDeleteRegarding the Gershenfeld's book "Fab", it's a very good read (and got me hooked on personal fabrication), but a little short on 3D printing. Which makes sense, because 3D printers (and material costs) were pretty expensive when he wrote the book; although fab@home's 3D printer brings the price down to under USD$1.5K, and we're shooting for under USD$500.
I think it would be a good move to work with the Fab Lab and Fab @ Home groups; we're reaching out to them and seeing if they're interested. I hope they are.
Regarding outlay, it's hard to say. ~$4K, with the CNC-ready Taig benchtop mill (aka instant RepStrap) weighing in at around $1250.
http://www.taigtools.com/mmill.html
***I was long thinking about the Lego idea (making a ( significant part of a) reprap from Lego parts), thought it 'too' somethingOrOther... how did LordCat get on?***
ReplyDeleteThe theory looks great... but... just like the rest of my reprap(s), the theroy is waiting until i get a proper match of motor <-> controller (currently I've got bipolar motors and a unipolar controller!)
I've only got it for one axis, and I don't have the threaded rod 'mounted' on anything yet, but it moves back and forth nice and smoothly when I attach it to a drill... With as great as the bricks work, I may just cap the ends with more lego bricks and figure out how to secure those down.
I do have some lego 'rack & pinion' sitting around somewhere that I was considering trying to use instead of a threaded rod, but I don't think I've got enough length to be of any use...
I've currently got a shipment of parts coming 'priority mail' that will hopefully get some motors up and running for me, so with luck I'll be posting some news next week!
***I wonder just what the current outlays of the various reprappers are? ... Is anyone keeping 'tabs'? I'm sure that time is the 'biggest' thing.. ***
ReplyDeleteYou'd be wrong. All those little visits to the hardware store, shopping at Mouser and buying "cheap" motors over the web really add up after a while. Right now I figure I've spent somewhere between $2500-3000.
Mind, I sat out to develop a bunch of new skills, like circuitry design and PIC programming. I've also learned how to fabricate steel, weld, run a drill press and a host of other things that I didn't know how to do before.
I wanted to get my head around pretty much all the skills necessary to doing this sort of thing, so that number shouldn't be taken to be what would be necessary for anyone else to put down to get into the game. I had ulterior motives in getting those skills so that I could take on some other projects as part of my consultancy business. It's been a very worthwhile experience for me.
***we're shooting for under USD$500.***
I'm shooting for about $125 for parts for mine. :-)
I am massively underwhelmed by both the FabLab and the Fab@home crowd. Their work strikes me as the usual sort of all flash and no substance bullshit that one always sees coming out of the Ivy League. They're really good at grabbing headlines and "appearing" to be at the cutting edge. When it comes down to making a lasting contribution, however, they just aren't there. That's why I'm opposed to getting RepRap involved with them.
***I think FabLab, w/ the branches 'round the world, are doing something good...***
ReplyDeleteGood luck on figuring out what that "something" actually is. :-/
Forrest,
ReplyDeleteI think you're being too harsh.
Evan and Hod seem like quite decent folk from our correspondence with them, and their 3D printer looks like a good solid project. For one thing, they've got two machines operating out in the wild:
http://128.253.249.235/wiki/index.php?title=Fab%40Home:Installations
Regarding MIT's Fab Lab, I know that another group of people at MIT behaved treacherously when you worked with them a long time ago, and I agree that the Media Lab tends to do more fluff than real work, but I think we should consider the MIT Center for Bits and Atoms and the MIT Fab Lab objectively.
I've had my say. I think there is more than enough to do in making all of aspects of reprap work properly without seeking out such colleagues. It would appear that many of you are, however, hot to go haring off in that direction. While I wish you good fortune I think that I'm going to give all that a pass. I'm just too old to happily chance repeating bad experiences.
ReplyDeleteHi everyone - I appreciate the generally favorable discussion of Hod's nature and my nature. I would be very happy to work with you RepRap lot once I get the last few bits of Fab@Home in place. By the way, our server has been reconfigured so many old links to the site will no longer work. The official URL is http://www.fabathome.org (or .net, .info, .com).
ReplyDeleteThanks!
Evan
This comment has been removed by the author.
ReplyDeleteCompleted last year, Lipson’s fabrication machine, called a “fabber,” can print thousands of three-dimensional objects, everything from toy parts to artificial muscles, using dozens of materials, including PlayDoh, peanut butter and silicone, by following simple directions sent to it by a PC. About the size of a microwave, the fabber costs $2,300 to assemble—roughly one tenth the cost of commercial 3-D printers.
ReplyDeleteThe Desktop Factory: Roboticist Hod Lipson wants you to stop shopping and use his portable 3-D printer to make your own stuff
About the Lego bootstrap idea, I have asked (May 31th 2007) for a new mindstorms specifically to try this possibility; if someone is trying too, please email to al.rivero@gmail.com. Also, I think that a mini-reprap aiming to build lego pieces would capture a huge userbase.
ReplyDelete