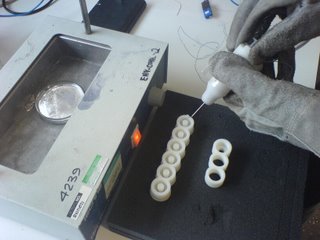
Apologies for the delay in posting this....
A few weeks ago I attempted to produce some bearings using Field's metal and RP moulds. The aim was to prove that it was possible for a RepRap machine to produce its own bearings, as Field's metal melts at approximately 70 degrees celcius......
I tried 2 methods
1. Casting the metal in a mould with the 8mm steel bar in situ, using silicone grease as a spacer.
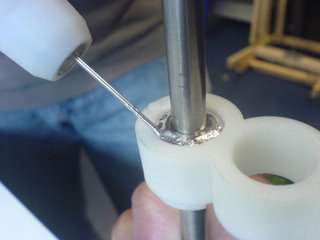
2. Casting the metal in a mould with a plug that could be hammered through once the metal had solidified.
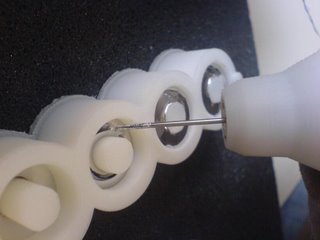
Method 1 failed as a bearing (but would be good as a locating/fixing mechanism - ie calibrate
machine, then set all joints in metal)
Method 2 produced some nice bearings..... (Only tested by hand so far)
The Moulds
Method 1 - 3 hole mould and cap used to locate the rod and seal the base.
Method 2 - 6 hole mould with varying plug diameters, the support material needs to be left on to hold the plug in place.
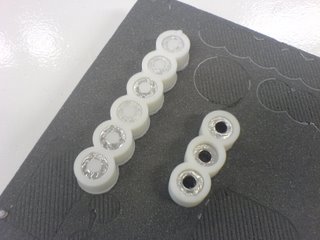

Moulds 1 & 2 and concentricity cap, and the finished bearings (before knocking through plugs)
The best results were achieved with a centre plug diameter of 8.2mm (to fit an 8mm bar)
Will be performing some basic tests on them this week
Fulll report available if anyone is interested
Method 1 failed as a bearing (but would be good as a locating/fixing mechanism - ie calibrate machine, then set all joints in metal)
ReplyDeleteFast thinking. Well done! :-D
That's interesting! So how does the Fields metal stand up as a bearing, does it wear well? In my limited experience, the hardest part is not basic fabrication of bearings and such, but getting the tolerances and surfaces good enough to get long lasting parts. But with a few well chosen tricks...
ReplyDeleteI suppose methode 1 failed because of thermal contraction. I've run into that with metal plugs surrouned by cast metal. In some cases it can be drilled out to size afterwards if the plug is pushed out.
BTW, glad to see this was attempted with a lead free alloy. :)
What would be the material cost per bearing here? Should be an easy calculation: ( Field Metal Cost / KG ) / ( Mass of bearing)
ReplyDeleteIs it price competitive with off the shelf bearings made from aluminum, brass, or steel?
Nice start, in any case.
Would it help to create the bearings in two halves? This eliminates the contraction stress and might allow the bearings to be poured in situ.
ReplyDeleteVik :v)
Vic, that's exactly how Babbitt bearings usually are made, there is a good description on Wikipedia.
ReplyDeleteI think straight Babbitt bearing emulation is rather labor intensive for the target RepRap concept though. Instead, I'd suggest experimenting pouring against a very smooth shaft, but with a cut at the top to allow contraction. I'd also suggest a very thin layer of Field's metal, supported by a strudy extruded plastic "pillow".
Maybe it could even be poured thin and flat, say on a piece of glass, then rolled to the desired diameter.
In any case, if the shaft is not perfectly smooth, nothing bearing-like will last very long. But that might be okay for some uses.
Think of how cool it would be if you could extrude a plaster or thin clay. Hands-free injected molding.
ReplyDeleteQuick question, while on the topic. How would plain rosin/silver core solder fare as an extrudable liquid?
As you know, solder is already in filament form :)
Actually...
ReplyDeletewhat about using a technique like this to make a threaded rod not threaded? Or to make a low-backlash nut... wrap a few turns of heavy-gauge solder around the rod, put a holdar around those... it's seeming to work when I try it. Also, wrapping molten solder around one of those multi-thread screw drives that come on the steppers I have results in a passable nut for them.