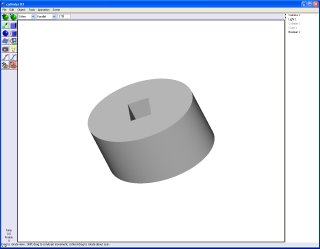
Afterwards, I exported the "design" as an STL file. Here you can see what the shaded solid in AoI looks like as a wire frame representation of its STL file.
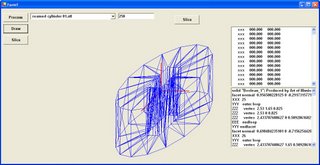
Then you can see what happens when you make multiple passes through the STL representation of the solid form with a cutting plane.
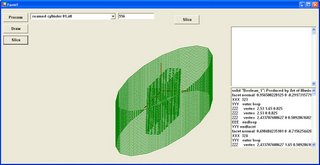
From there we start mapping paths for the Mk II to extrude the solid.
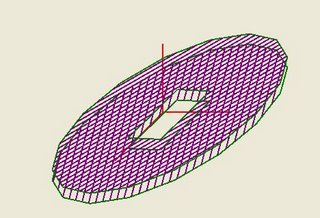
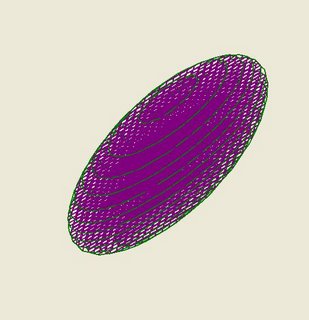
The code looks fairly robust so far. Mind, I haven't attempt to correct for pixel geometry yet.
Wow, looks like you are moving right along there...
ReplyDeleteHaving a background in 3D illustration and animation, I'm wondering what you mean by "pixel geometry"?
***I'm wondering what you mean by "pixel geometry"?***
ReplyDeleteI'm referring to the 2D proportions of a pixel on a screen. It's rarely square, so you tend to have to compensate for it in your coding at times.
Oh, I see, you mean at the display. I'm guessing this doesn't interact with slices and paths and such. That's what I couldn't figure out!
ReplyDeleteOn a totally different topic, I got tired of dodging wafts of solder fumes. (Now where did I read you and Adrian posting about that...?)
In any case, I salvaged our old kitchen stove ventilator and thanks to an outside vented flex pipe, it's doing a great job in the workshop now. Also sucks out glue fumes (been testing molten plastic against silicone, very non-stick...) or anything that might bug someone in the house...